In today's industrial world, competition is more intense than ever before. Companies involved in machinery and equipment manufacturing are under constant pressure to maximize efficiency, reduce costs and minimize downtime. One of the most advanced ways to achieve these goals is to implement a condition monitoring system. In this blog post, we will look at the benefits of condition monitoring in detail and explain why this technology is an indispensable part of modern industrial processes.
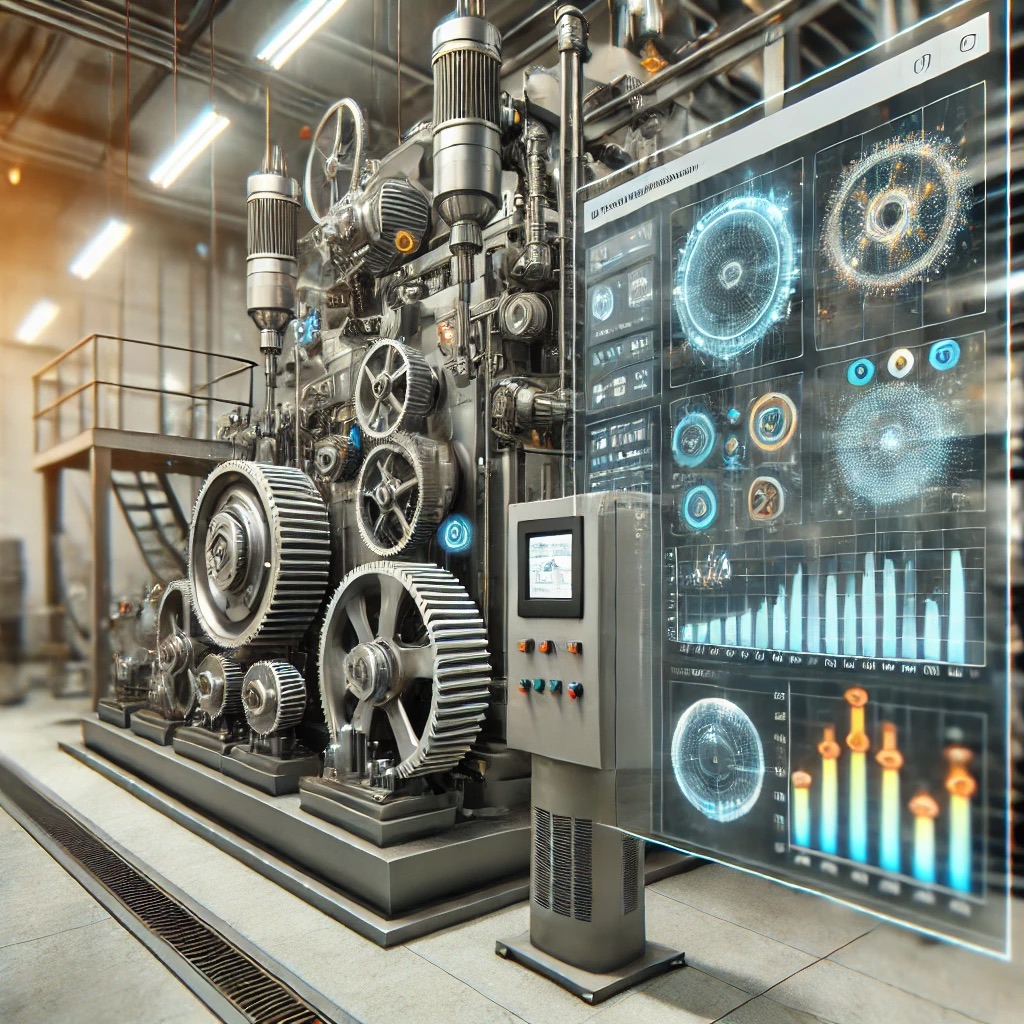
1. What is condition monitoring?
Condition monitoring is the process of monitoring the condition of machinery and equipment in real time to detect signs of wear or potential failure at an early stage. By using sensors to monitor various operating parameters such as temperature, vibration, pressure and more, companies can take preventative action before costly breakdowns occur.
1.1 Historical development
Condition monitoring has its roots in the industrial revolution, when the first methods for monitoring machine conditions were developed. Over time, technologies have evolved and today advanced systems such as predictive maintenance and artificial intelligence (AI) are integral parts of modern condition monitoring solutions. You can find more information on historical developments and trends in customer service in our article “The trends in customer service: digitization as the key to the future”.
2. Advantages of condition monitoring
The implementation of condition monitoring systems offers a wide range of benefits that go far beyond pure condition monitoring. These benefits extend to various areas of the business and help to increase efficiency and profitability.
2.1 Reduction of downtime
One of the biggest challenges in mechanical and plant engineering is unplanned downtime, which can cause considerable costs. By continuously monitoring the condition of the machine, anomalies can be detected at an early stage and maintenance work can be planned before a breakdown occurs. This not only significantly reduces downtime, but also the associated costs. For more information on the costs and impact of downtime, see our article “The large losses from downtime in manufacturing plants”.
2.2 Extending the service life of machines
By detecting wear and other problems at an early stage, targeted maintenance measures can be taken that significantly extend the service life of machines. This leads to a better return on investment and reduces the need to invest in new machines. The benefits of service life extension are an important aspect of modern maintenance strategies and can be further enhanced in conjunction with predictive maintenance.
2.3 Improving operational efficiency
Condition monitoring enables companies to optimize their operations by gaining insights into the performance of their machines and systems in real time. By analyzing the collected data, bottlenecks can be identified and eliminated and processes can be continuously improved. These efficiency gains are crucial for success in a competitive market. Find out more about the optimization potential in our article “5 ways you can optimize your customer service processes”.
2.4 Increasing safety
Machines and systems that are not properly maintained can pose a significant safety risk. Condition monitoring helps to identify potential sources of danger at an early stage and prevent accidents by ensuring that safety-critical components are serviced or replaced in good time. This not only contributes to the safety of employees, but also reduces the risk of production interruptions.
2.5 Cost savings through predictive maintenance
One of the biggest financial benefits of condition monitoring is the ability to reduce maintenance costs. Instead of carrying out maintenance work according to a fixed schedule, condition monitoring enables needs-based maintenance that is tailored to the actual condition of the machines. This reduces unnecessary maintenance work and saves costs.You can find out more about how condition monitoring works in practice in our article “Avoiding machine downtime with condition monitoring”.
3. Areas of application for condition monitoring
Condition monitoring can be used in a wide range of industrial applications, from manufacturing to power generation and aviation. In this section, we take a look at some of the most important application areas.
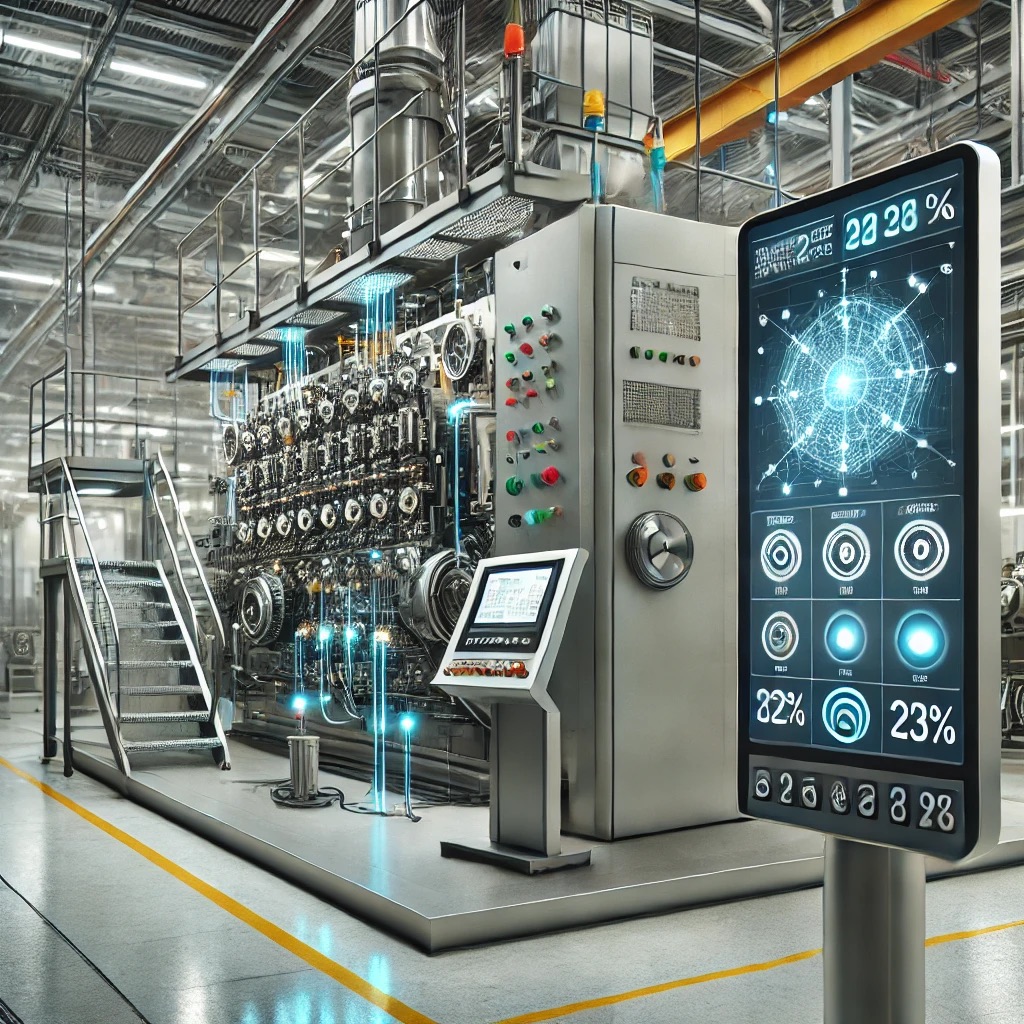
3.1 Manufacturing industry
In the manufacturing industry, condition monitoring is essential to maximize the efficiency of production lines and minimize unplanned downtime. By monitoring key parameters, companies can ensure that their machines are operating at optimum performance. For more insights into the application of condition monitoring in manufacturing, read our article “Monitoring complete plants and production lines remotely”.
3.2 Power generation
In power plants and other energy generation facilities, equipment reliability is critical. Condition monitoring helps to identify potential problems at an early stage and ensure that the equipment operates continuously and efficiently.
3.3 Aerospace
In the aerospace industry, condition monitoring plays a crucial role in ensuring the safety and reliability of aircraft. By monitoring critical components, failures can be avoided and passenger safety ensured.
3.4 Oil and gas industry
In the oil and gas industry, where machines often operate in extreme conditions, condition monitoring is invaluable. It allows equipment to be monitored in real time and helps to avoid costly breakdowns.
4. Condition monitoring technologies and methods
Condition monitoring encompasses a range of technologies and methods that work together to accurately monitor the condition of machinery and equipment. In this section, we will look at some of the most important technologies and methods.
4.1 Sensors and data acquisition
Sensors are at the heart of every condition monitoring system. They continuously collect data on various operating parameters such as temperature, vibration, pressure and more. This data is then analyzed in real time to identify potential problems.
4.2 Data analysis and processing
The collected data is analyzed using advanced algorithms and artificial intelligence (AI). This analysis makes it possible to identify patterns and anomalies that could indicate impending failures. Find out more about the role of AI in our article “Artificial intelligence in customer service: an opportunity for the industry”.
4.3 Remote monitoring
Modern condition monitoring systems enable machines and systems to be monitored remotely so that maintenance teams can identify and rectify problems without having to be on site. This saves time and money and enables a faster response to potential problems. You can find more information on remote monitoring in our article “Technical solution for remote commissioning of machines and systems”.
4.4 Integration with other systems
Condition monitoring systems can be seamlessly integrated into other industrial systems such as enterprise resource planning (ERP) and asset management systems. This enables a holistic view of operations and optimized decision making.
5. Implementing a condition monitoring system
Implementing a condition monitoring system requires careful planning and execution. This section discusses the key steps and considerations when implementing such a system.
5.1 Needs analysis
The first step in implementing a condition monitoring system is a thorough needs analysis. It is important to understand which machines and systems need to be monitored and which parameters are most important. You can find out more about how to ensure a successful implementation in our article “5 steps to implementing a condition monitoring system”.
5.2 Selecting the right technology
Choosing the right sensors and data analysis tools is critical to the success of the condition monitoring system. It is important to choose technologies that meet the specific requirements of your business.
5.3 Integration into existing systems
Integrating the condition monitoring system into existing industrial systems is an important step. It is important to ensure that the new system works seamlessly with existing processes and technologies.
5.4 Staff training
Successful implementation also requires the training of personnel working with the new system. This ensures that employees are able to use the system effectively and take full advantage of its benefits. You can find more information on training and support in our article “Training, education and training with remote support”.
6. Challenges and solutions during implementation
As with any new technology, there are challenges that need to be overcome when implementing condition monitoring systems. This section discusses some of these challenges and possible solutions.
6.1 Costs and budgeting
One of the biggest challenges when implementing a condition monitoring system is the cost. It is important to weigh the long-term savings from reduced downtime and extended machine life against the initial investment.
6.2 Data management
Collecting and processing large amounts of data can be a challenge. It is important to ensure that the right tools and processes are in place to effectively manage and analyze the data.For more information on the latest developments in data management, read our article “Industry 4.0: What it means for customer service and after-sales support”.
6.3 Integration and compatibility
The integration of the new condition monitoring system into existing IT infrastructures can be complex. It is important to ensure that the system is compatible and fits seamlessly into existing processes.
6.4 Security
The security of the data collected is another important concern. It is crucial that the system implements robust security measures to ensure the integrity and confidentiality of the data.
7. Future prospects for condition monitoring
Condition monitoring will continue to play a key role in the industry in the future.
In this section, we take a look at the future developments and trends that will shape condition monitoring.
7.1 Artificial intelligence and machine learning
With the advent of artificial intelligence and machine learning, condition monitoring will become even more precise and effective. These technologies make it possible to analyze data in greater depth and predict failures with a high degree of accuracy.
7.2 Integration with the Internet of Things (IoT)
The integration of condition monitoring with the Internet of Things (IoT) opens up new possibilities for monitoring and controlling machines in real time. IoT enables even more comprehensive networking and data analysis, which will lead to further improvements in operating processes. You can find out more about IoT and its impact on customer service in our article “How IoT is revolutionizing customer service”.
7.3 Advanced remote maintenance
With the further development of remote maintenance technologies, it will be possible to carry out even more complex maintenance tasks remotely. This will further increase efficiency and reduce the need for on-site visits. You can find an interesting example of the use of remote maintenance in our Customer Success Story with Evonik.
7.4 Sustainability
In the future, condition monitoring will also play an important role in promoting sustainability in the industry. By optimizing energy consumption and reducing waste, condition monitoring will help to reduce the environmental impact. Learn more about the importance of digitalization and sustainability in mechanical engineering in our article “With retrofit to digitalization and sustainability in mechanical engineering”.
8 Conclusion: Condition monitoring as the key to success
Condition monitoring offers companies in the mechanical and plant engineering sector numerous benefits, from reducing downtimes and extending the service life of machines to increasing operational efficiency and safety. These benefits contribute directly to a company's competitiveness and profitability. If you are considering implementing a condition monitoring system in your business, now is the time. Technology is constantly evolving, offering more and more opportunities to optimize your operations and reduce costs.
Learn more about the benefits and possibilities that condition monitoring offers and let's take your company's efficiency and sustainability to the next level together.
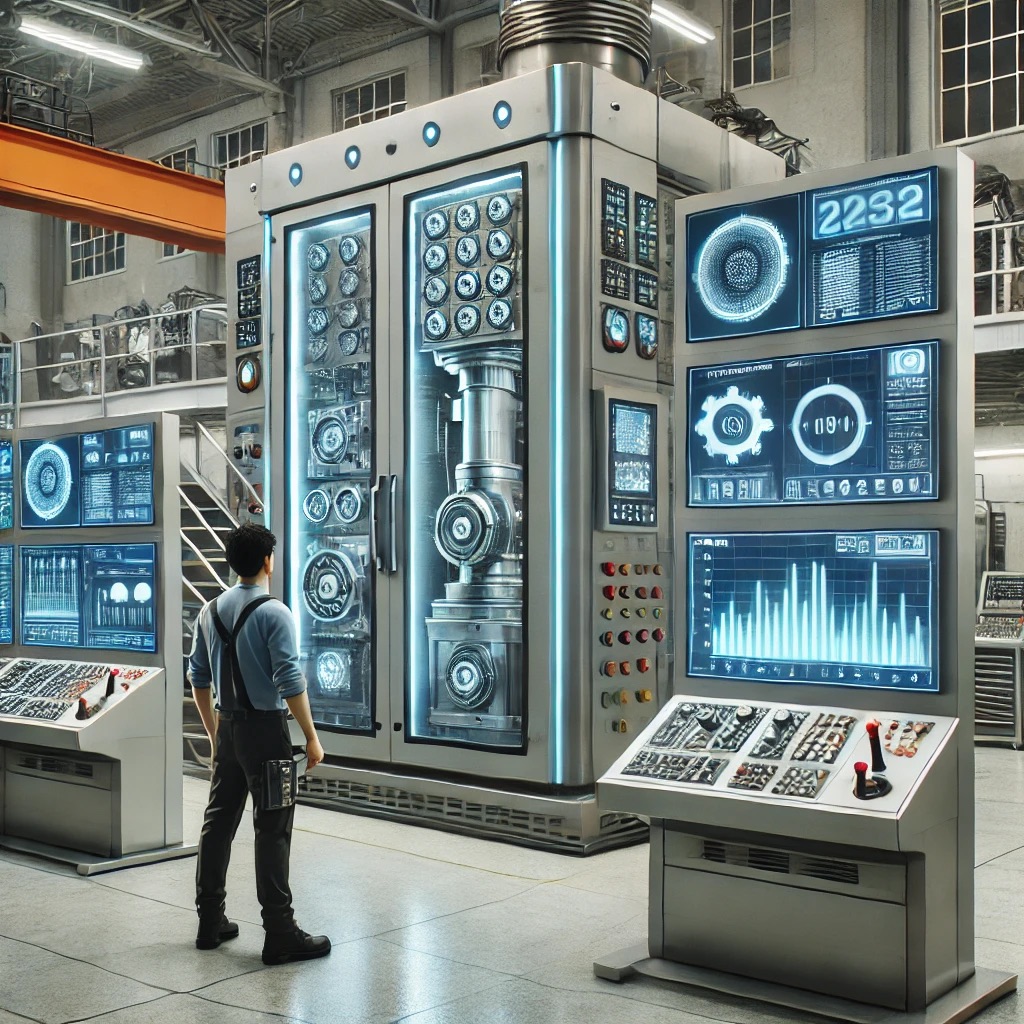
By considering these solutions, you can take an important step towards a future-oriented, efficient and sustainable business. Don't miss the opportunity to take full advantage of condition monitoring - contact us today!
Internal links in this article:
- “The big losses caused by downtime in production plants”
- “Predictive maintenance“
- “5 ways you can optimize your customer service processes”
- “Avoiding machine downtime with condition monitoring”
- “Monitoring complete systems and production lines remotely”
- “Artificial intelligence in customer service: an opportunity for industry”
- “Technical solution for the remote commissioning of machines and systems”
- “5 steps to introducing a condition monitoring system”
- “Industry 4.0: What it means for customer service and after-sales support”
- “Training and further education with remote support”
- “How IoT is revolutionizing customer service”
- “With retrofit to digitalization and sustainability in mechanical engineering”