Introduction
In the modern manufacturing industry, machine downtime is a costly problem that can cost companies a lot of money. To minimize this downtime and maximize efficiency, condition monitoring is an indispensable tool. In this article, we will dive deep into the topic of condition monitoring and show how it helps to prevent machine downtime. We will use the wide range of services and products available on ADTANCE to illustrate practical applications and solutions.
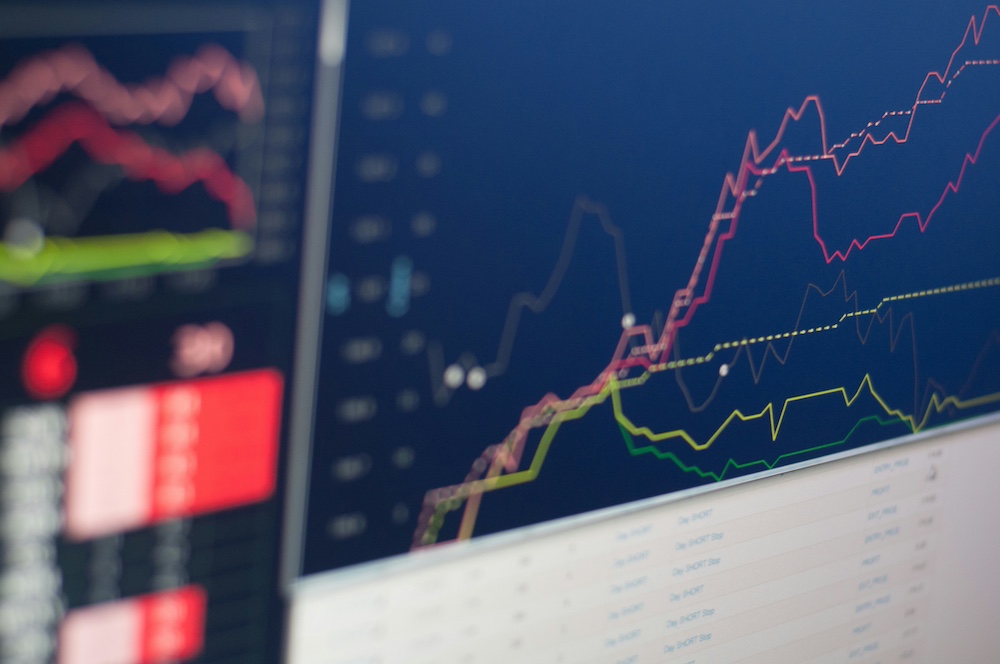
What is condition monitoring?
Condition monitoring refers to the continuous monitoring of the condition of machines and systems during operation. The aim is to identify potential problems at an early stage and take action before costly breakdowns occur. This proactive maintenance strategy can help companies to extend the service life of their machines and reduce operating costs.
Advantages of condition monitoring
- Early detection of problems: Continuous monitoring allows problems to be detected before they lead to major breakdowns.
- Cost reduction: Avoidance of unplanned downtime and associated high costs.
- Increased efficiency: Optimization of maintenance processes and reduction of downtime.
- Extending the service life of machines: Regular monitoring and maintenance lead to longer machine service life.
Condition monitoring techniques and tools
There are various techniques and tools that are used in condition monitoring to monitor the condition of machines. These include:
- Vibration analysis
- Thermography
- Ultrasonic testing
- Oil analysis
- Electrical tests
Vibration analysis
Vibration analysis is one of the most frequently used techniques in condition monitoring. It makes it possible to detect imbalances, misalignments, bearing problems and other mechanical faults.
Thermography
Thermography uses infrared cameras to visualize the temperature distribution on the surface of machines. Overheating can indicate problems such as electrical faults or friction.
Ultrasonic testing
Ultrasonic testing is used to monitor acoustic emissions from machines. This technique is particularly useful for detecting leaks and electrical discharges.
Oil analysis
Oil analysis monitors the condition of the lubricant in machines. Changes in the composition of the oil can indicate wear or contamination.
Electrical tests
Electrical testing includes monitoring current and voltage values and analyzing motor current signatures to detect electrical and mechanical pro
Implementing a condition monitoring solution
The implementation of a condition monitoring solution requires careful planning and consideration of several factors. Both technical and organizational aspects play a role.
Steps for implementation
- Determination of requirements
- Selection of suitable technologies
- Integration into existing systems
- Training of personnel
- Continuous monitoring and adaptation
Determination of requirements
The first step in implementation is to determine requirements. It is important to understand exactly which machines and processes are to be monitored and what objectives are being pursued with the monitoring.
Selection of suitable technologies
Based on the results of the needs assessment, the appropriate technologies and tools for condition monitoring can be selected. A thorough evaluation of the available options is crucial here.
Integration into existing systems
The integration of condition monitoring systems into the company's existing IT and OT infrastructures is a critical step. This includes connecting to existing SCADA or ERP systems and ensuring seamless data communication.
Staff training
An often overlooked but crucial aspect is staff training. Only with sufficient training can staff use the new systems effectively and interpret the monitoring data correctly.
Continuous monitoring and adjustment
After implementation, it is important to continuously monitor the systems and make adjustments where necessary. This ensures that the condition monitoring solution remains effective in the long term.
Practical examples and success stories
Customer service 4.0 with ADTANCE Support
A good example of the successful implementation of condition monitoring is the use of ADTANCE Support. This solution enables companies to take their customer service to the next level and avoid machine downtime through proactive monitoring.
Digitalization in service: After-Sales Service 4.0
Digitalization in service is another example of how modern technologies can be used to optimize customer service and minimize downtime. By using digital tools, service processes can be made more efficient and problems can be solved more quickly.
The importance of after-sales service in the industry
Good after-sales service is of great importance in industry. The importance of after-sales service shows how continuous support and monitoring can increase customer satisfaction and reduce machine downtime.
Technical solutions for the Industry 4.0 era
With Technical Solutions of the Age of Industry 4.0, companies can optimize their production processes and minimize downtimes. Condition monitoring is a central component of these solutions and helps to increase efficiency an
The role of predictive maintenance
Predictive maintenance is an advanced form of condition monitoring. It uses data analysis and machine learning to make predictions about the condition of machines and plan maintenance work in advance.
Advantages of predictive maintenance
- Proactive maintenance: Maintenance work can be planned and carried out before breakdowns occur.
- Cost savings: Reduction in maintenance costs by avoiding unplanned downtime.
- Efficient use of resources: Optimization of the use of maintenance personnel and materials.
Implementation of predictive maintenance
The implementation of predictive maintenance requires careful planning and the integration of various technologies. However, successful implementation can bring significant benefits and increase the reliability of production facilities.
Case studies
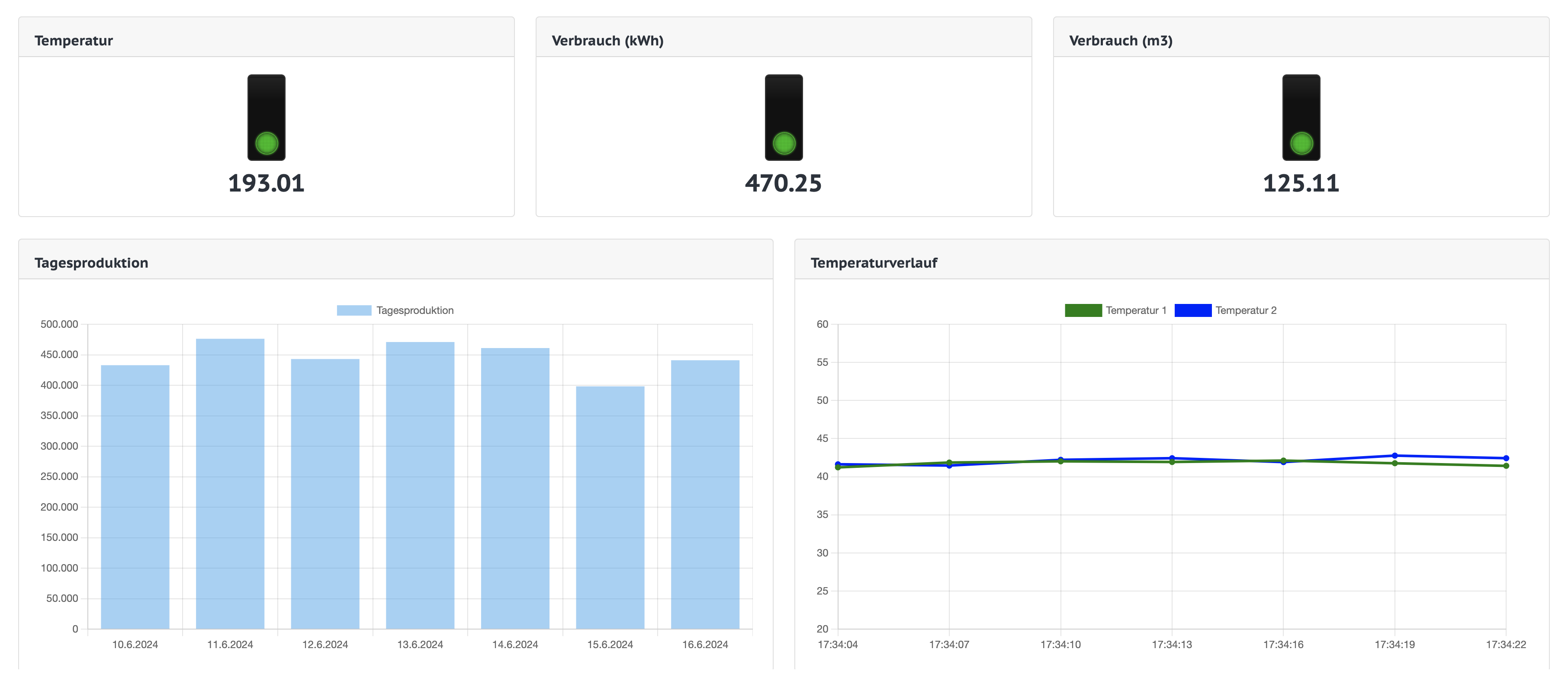
Evonik
The Customer Success Story with Evonik shows how the use of smart solutions has maximized machine uptime and reduced maintenance costs.
FRIMO
The Customer Success Story with FRIMO also clearly shows how the integration of solutions has prevented machine downtimes and increased efficiency.
Leser
The Customer Success Story with LESER illustrates how the use of modern monitoring technologies has optimized production processes and reduced downtimes.
Future
The future of condition monitoring and predictive maintenance is promising. With advancing digitalization and the integration of artificial intelligence, these technologies are becoming increasingly powerful and accessible.
Artificial intelligence in customer service
Artificial intelligence in customer service offers new opportunities to avoid machine downtimes and increase the efficiency of maintenance processes. By using AI, problems can be identified more quickly and solutions implemented more effectively.
Industry 4.0
Industry 4.0 is driving forward the networking of machines and systems. Condition monitoring and predictive maintenance play a central role in optimizing production and minimizing downtimes.
Future-oriented service
A future-oriented service relies on modern technologies and innovative approaches to improve customer service and avoid machine downtime. By integrating remote support and digital solutions, problems can be solved faster and operational efficiency increased.
Conclusion
Machine downtime is a serious problem for companies in the manufacturing industry. However, by using of condition monitoring and predictive maintenance, however, these downtimes can be effectively minimized. Modern technologies and digital solutions offer a wide range of opportunities to increase efficiency and reduce costs. While implementation requires careful planning and staff training, the long-term benefits are enormous.
From vibration analysis and thermography to the integration of artificial intelligence, there are numerous techniques and tools available to continuously monitor the condition of machines and proactively carry out maintenance work. Success stories from the field show how companies can use these technologies to optimize their production processes and increase customer satisfaction.
Overall, condition monitoring is an indispensable strategy for avoiding machine downtime and maximizing efficiency in the manufacturing industry. The future promises further exciting developments that will make these technologies even more powerful and accessible.
Contact us and implement your own condition monitoring solution.