The introduction of a Condition Monitoring Systems is a crucial step for companies in the mechanical and plant engineering sector to maximize the efficiency of their maintenance strategies and minimize downtimes. You know how important it is to ensure machine availability and optimize operating costs. This article provides you with a detailed five-step guide to successfully implementing a condition monitoring solution, without going into detail about external sensors.
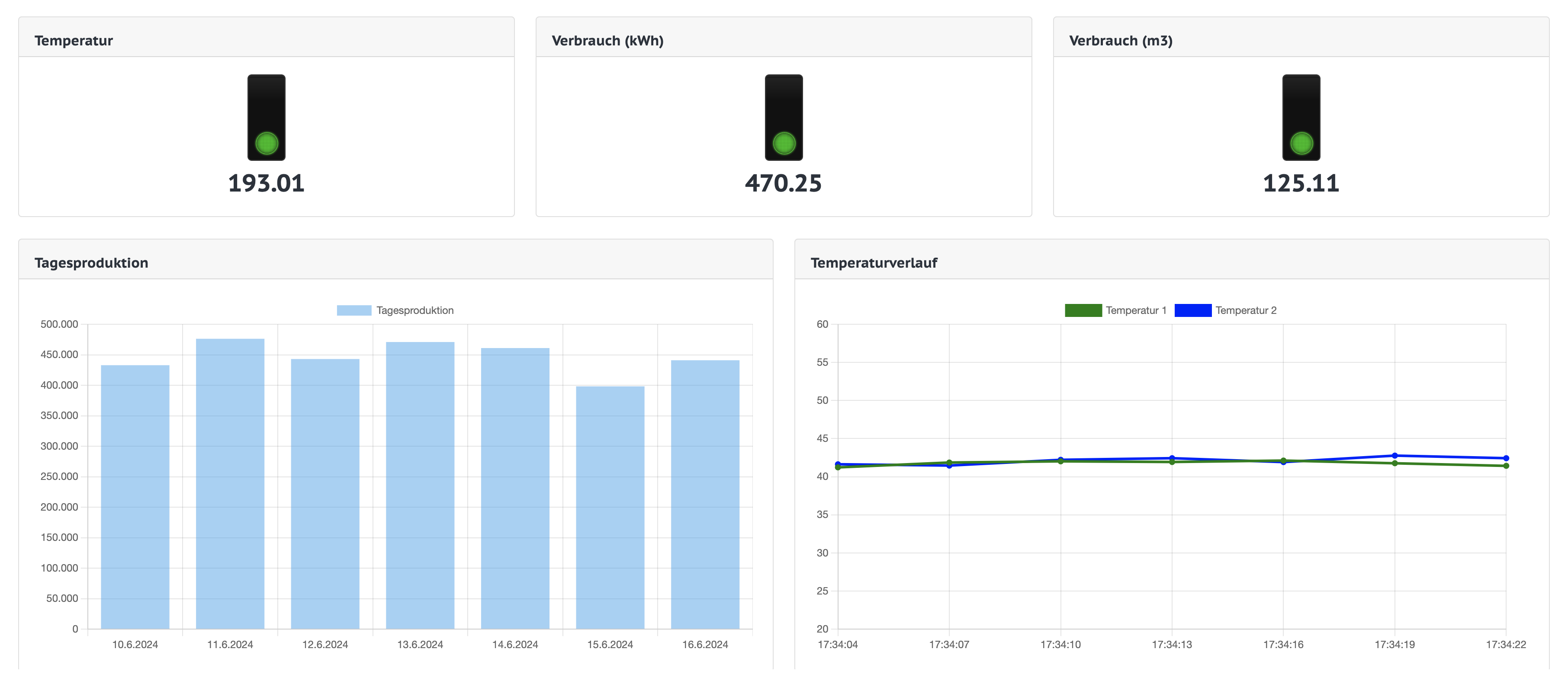
Step 1: Analysis and objectives
Analysis
The first step in introducing a condition monitoring system is to carry out a comprehensive analysis of your existing machines and systems. This includes:
-
Recording the machines and systems: Identify all relevant machinery and equipment in your operation that should be monitored. Create a detailed list that includes information such as manufacturer, model, year of manufacture, technical specifications and previous maintenance history.
-
Current condition analysis: Document the current condition of each machine. This can be done through inspections, maintenance reports and existing operating data. The aim is to obtain a clear picture of the initial condition.
-
Determine critical machines: Determine which machines are most critical to the production process. These machines should be the focus of the condition monitoring solution, as their failure can have a significant impact on production.
Objectives
Once you have carried out a thorough analysis, it is important to define clear objectives for condition monitoring:
-
Reduce unplanned downtime: A main objective could be to reduce the number unplanned-downtime by detecting potential problems at an early stage.
-
Extending machine life: Continuous monitoring and timely maintenance activities can extend machine life.
-
Cost savings: Long-term cost savings through reduced maintenance costs and avoided production downtime are also an important goal.
-
Improvement of maintenance planning: Optimization of maintenance intervals through the use of condition data to better plan preventive maintenance activities.
Step 2: Selecting suitable monitoring methods
In the next step, you must select the appropriate monitoring methods that are suitable for your specific machines and systems. Without going into external sensors, the following methods can be considered:
Using existing data sources
-
Machine data analysis: Many modern machines and systems already have integrated data sources such as control systems and internal sensors. This data can be used to monitor the condition of the machines.
-
Historical operating data: Analyze historical operating data to identify patterns and trends that could indicate upcoming problems.
-
Maintenance reports: Utilize existing maintenance reports and inspection data to identify anomalies and recurring issues.
Methods for data analysis
-
Vibration analysis: Analyze vibrations and oscillations generated by machines to detect deviations from normal conditions.
-
Thermography: Monitor temperature distribution on machine surfaces to identify hotspots and unusual heating.
-
Acoustic analysis: Use noise and ultrasound to detect changes in machine acoustics that could indicate mechanical problems.
-
Oil analysis: Examine the lubricating oil for contaminants and wear particles to monitor the condition of bearings and gears.
Step 3: Implementing the software and data infrastructure
The implementation of a powerful condition monitoring system requires a robust software and data infrastructure. This step is crucial to effectively process and analyze the collected data.
Selection of condition monitoring software
-
Define requirements: Based on your goals and the selected monitoring methods, you should clearly define the requirements for the condition monitoring software. Consider aspects such as user-friendliness, scalability and integration with existing systems.
-
Software evaluation: Conduct a market analysis to identify suitable condition monitoring software solutions. Also consider references and experience reports from other companies in the mechanical and plant engineering sector.
-
Pilot project: Start with a pilot project to test and evaluate the selected software on a smaller scale. This helps to identify potential problems at an early stage and make adjustments.
Data infrastructure
-
Data integration: Integrate the various data sources into a central database. This can be done by using industry protocols and interfaces such as OPC UA, Modbus or proprietary interfaces of the machine manufacturers.
-
Data processing: Ensure that data can be processed and analyzed in real time. This requires powerful servers and database solutions.
-
Security and data protection: Implement measures to ensure data integrity and protect sensitive information. This includes the use of encryption technologies and access management systems.
Step 4: Staff training and involvement
A decisive success factor for the introduction of a condition monitoring system is the involvement and training of staff. Only a well-trained and motivated team can exploit the full potential of condition monitoring software.
Training measures
-
Develop training concepts: Create training concepts that are tailored to the various target groups, e.g. operating personnel, maintenance staff and managers. The training should include both theoretical and practical content.
-
Training on the job: Conduct Training directly on the machines to familiarize personnel with the practical application of the condition monitoring solution. Use real use cases and examples from your own operations.
-
Certifications: Offer certifications to increase staff motivation and ensure the quality of training.
Involvement of the staff
-
Communication: Inform the entire team early on about the introduction of the condition monitoring system and the associated benefits. Transparent communication helps to reduce potential concerns and create acceptance.
-
Involve employees: Actively involve staff in the implementation process. Use their experience and knowledge to tailor the condition monitoring system to the specific requirements of the business.
-
Establish a feedback culture: Encourage a feedback culture where employees can contribute their experiences and suggestions for improvement. This helps to continuously optimize the monitoring system and adapt it to the needs of the company.
Step 5: Continuous improvement and optimization
After the successful implementation of the condition monitoring system, it is important to establish a process of continuous improvement and optimization. This ensures that the monitoring system remains effective in the long term and adapts to changing conditions.
Monitoring and analysis
-
Regular review: Continuously monitor the performance of condition monitoring and regularly review the data collected and its analysis.
-
Trend analysis: Perform trend analyses to identify long-term developments and proactively respond to potential problems.
-
Benchmarking: Compare the results of your condition monitoring system with industry best practices and benchmarks to identify potential for improvement.
Optimization of the system
-
Software updates: Always keep the monitoring software up to date and regularly use updates and extensions offered.
-
Adaptation of monitoring methods: Continuously adapt the monitoring methods used to new findings and technological developments.
-
Employee training: Conduct regular refresher training to ensure staff are up to date and can use the systems effectively.
Performance review
-
Key figures and KPIs: Define clear Key figures and key performance indicators (KPIs) to measure the success of condition monitoring. Examples include reducing unplanned downtime, reducing maintenance costs and increasing machine availability.
-
Regular reporting: Create regular reports and presentations to transparently show the results of the condition monitoring solution and illustrate the benefits for the company.
-
Adjustment of objectives: Regularly review the original objectives and adjust them as necessary to meet changing requirements and conditions.
Conclusion
The introduction of a Condition Monitoring System in mechanical and plant engineering is a complex process, but one that can offer considerable advantages for maintenance and operation. Through a thorough inventory, the selection of suitable
monitoring methods, implementing a robust data infrastructure, training and involving personnel, and continuous improvement and optimization, companies can increase their machine availability, reduce maintenance costs and minimize unplanned downtime.
The five steps to implementing a condition monitoring system, as described in this article, provide a practical guide to making this process a success. As the person responsible for maintenance, it is your responsibility to actively shape this change and support your team along the way. Take advantage of the opportunities offered by a condition monitoring system and drive digitalization and increased efficiency in your company.