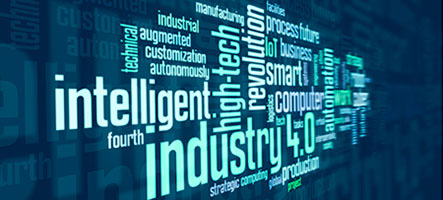
In the midst of a rapidly evolving technological landscape, industry 4.0 has emerged as a term synonymous with the future of manufacturing and production. This fourth industrial revolution isn't just a buzzword; it signifies a fundamental shift in the way we create, manage, and distribute goods, blending traditional manufacturing techniques with smart technology to drive unprecedented levels of efficiency and innovation.
The Genesis of Industry 4.0
The term Industry 4.0 first made its appearance at the Hannover Fair in Germany in 2011. It referred to a government initiative aimed at computerizing manufacturing, a strategic move to ensure Germany's future as a leading player in industrial manufacturing.
This term has since been adopted worldwide to describe the digitization and interconnection of industrial processes, spanning from production to customer service. It signifies a shift towards "smart factories" that leverage Information and Communication Technology (ICT) to optimize production processes and improve efficiency.
The Four Pillars of Industry 4.0
To understand Industry 4.0, we need to delve into its four fundamental pillars:
-
Interconnection: In an Industry 4.0 framework, machines, devices, sensors, and people connect and communicate with each other. The seamless flow of information allows for more precise and timely decision-making.
-
Information Transparency: With advancements in sensor technology and data collection methods, companies have access to vast amounts of operational and performance data. This data can be used to create a virtual copy of the physical world - a Digital Twin, enabling better understanding and modeling of processes.
-
Technical Assistance: Systems equipped with AI and machine learning capabilities can assist humans in making informed decisions and solving complex problems. Furthermore, these systems can perform tasks that are unsafe or uncomfortable for human workers.
-
Decentralized Decisions: In Industry 4.0, cyber-physical systems have the ability to make simple decisions on their own. This allows for more flexibility and responsiveness in production processes.
Industry 4.0 has the potential to revolutionize the industrial sector. With the fusion of digital and physical technologies, the boundaries between the physical and virtual world are blurring.
Industry 4.0 has vast implications for various sectors, including customer service. As businesses transition towards digitized, automated, and interconnected operations, customer service must also evolve. Traditional, reactive approaches to customer service are being replaced by proactive and predictive models, enabled by technologies such as AI, data analytics, and digital twins.
Industry 4.0 and The Evolution of Customer Service
The principles of Industry 4.0 have not just transformed the way we manufacture goods but also redefined the way companies approach customer service. In this section, we'll explore how the customer service landscape has been shaped by the tenets of Industry 4.0, giving rise to the concept of Service 4.0.
From Reactive to Proactive Customer Service
Traditional customer service models were primarily reactive. However, the digital transformation brought about by Industry 4.0 enables a more proactive approach. By leveraging data analytics, businesses can anticipate customer needs and address them before they become issues. This proactive customer service helps increase customer satisfaction and loyalty while reducing service costs.
Enhancing Support with AI and Machine Learning
Artificial intelligence and machine learning, two key components of Industry 4.0, play crucial roles in transforming customer service. They help automate and streamline various aspects of service delivery, reducing human errors, and improving efficiency. For example, AI can help create AI-supported checklists and instructions, enabling faster, more efficient customer support.
The Rise of Remote Support
Another notable development in the customer service sector is the rise of remote support. With the help of advanced technologies, businesses can now provide real-time support to their customers from afar, eliminating the need for on-site visits. This remote support approach not only reduces service delivery costs but also provides faster and more efficient support.
Predictive Maintenance with IoT and Big Data
Predictive maintenance, another facet of Service 4.0, leverages the Internet of Things (IoT) and big data to predict and prevent equipment failure. By collecting and analyzing data from connected devices, businesses can anticipate potential issues and address them before they lead to equipment failure. This approach reduces downtime, saves costs, and improves the overall quality of customer service. Learn more about this approach in our article on predictive maintenance.
The integration of digital technologies in customer service is revolutionizing the way businesses interact with their customers. Companies that embrace Service 4.0 will set new standards in customer experience.
As we delve deeper into the era of Industry 4.0, businesses must adapt their customer service strategies to stay competitive. By leveraging the principles of Industry 4.0, companies can improve customer satisfaction, reduce costs, and increase efficiency.
The Role of Customer Portals in Industry 4.0
The evolution of Industry 4.0 hasn't merely digitalized production lines, but it has also transformed how businesses interact with customers. A prime example of this transformation is the emergence of customer portals.
Empowering Customers Through Digital Portals
Customer portals represent the future of customer interaction and engagement. They provide a personalized, easy-to-use platform where customers can access relevant information, submit service requests, and engage with service providers. Businesses that have implemented a customer portal found that it enhances customer satisfaction, improves service efficiency, and reduces administrative costs.
Customer portals bridge the gap between businesses and customers. They empower customers by providing them with the tools and information they need to self-serve, resulting in higher customer satisfaction rates.
Our article on implementing a customer portal discusses how such a system can be set up effectively.
Augmenting Reality for Enhanced Service
Another remarkable application of Industry 4.0 technologies in customer service is the use of Augmented Reality (AR). AR provides an immersive, interactive platform that allows technicians to visualize complex processes, enhancing their ability to troubleshoot issues remotely. This method can significantly improve service efficiency and customer satisfaction. Learn more about this in our article on augmented reality.
How does Industry 4.0 promote a resource-efficient circular economy through data-driven assessment of products throughout their lifecycle?
Industry 4.0 is revolutionizing the way companies approach sustainability by promoting a resource-efficient circular economy. This innovative industrial wave integrates advanced data analytics to review products throughout their lifecycle. Right from the initial design stage, careful consideration is given to how each component can be optimally reused or recycled. This methodology ensures that materials are not only used efficiently, but also contribute to an ongoing cycle of reuse, reducing waste and promoting sustainability. The insights gained through data over the life of a product help to refine future designs and close the loop of the product life cycle in an environmentally conscious way.
How can optimized logistics processes benefit from intelligent networking, especially in terms of ideal delivery routes and automatic material replenishment?
Optimized logistics through intelligent networking:
Smart networking significantly improves logistics operations by introducing two key efficiencies: the calculation of ideal delivery routes and the automation of material replenishment.
1. Ideal delivery routes:
Intelligent algorithms play a crucial role in logistics by calculating the most efficient routes for delivery. This optimization not only reduces travel time, but also fuel consumption, thereby lowering operating costs and environmental impact.
2. Automatic material replenishment:
Automating material replenishment is another area where intelligent networking shines. Machines within the network are designed to monitor their own material levels and automatically send alerts when they need to be replenished. This real-time monitoring ensures that there are no delays due to material shortages, keeping the supply chain moving and reducing downtime.
By utilizing intelligent networks, logistics systems are not only reactive but also proactive, dynamically adapting to both immediate demands and foreseeable needs. This results in streamlined operations that save time, costs and resources, making companies more competitive and adaptable to market changes.
How will production lines evolve in the future with the concept of modular setups for improved productivity and cost efficiency?
The future development of production lines
Production lines are facing significant changes in the coming years, with the trend moving towards modular facilities. This development is expected to fundamentally change the way industries manage assembly and production operations.
Advantages of modular design:
-
Flexibility and adaptability: Modular production lines are designed to be quickly assembled, reconfigured or disassembled to meet specific tasks or product requirements. This flexibility allows manufacturers to efficiently switch between processes or update their production capacity without extensive downtime.
-
Increased productivity and cost-effectiveness: By integrating modular systems, production lines can improve both productivity and economic efficiency. This setup reduces wasteful processes and minimizes the resources needed for reconfiguration, resulting in significant cost savings.
-
Customization and small batch production: Modular facilities enable the production of bespoke or individualized products in smaller quantities. This capability ensures that manufacturers can meet specific customer requirements without the need for large production runs, making customized products more affordable and accessible.
These advances suggest that the future of manufacturing will be more dynamic, with a strong emphasis on efficiency and the ability to respond quickly to changing market demands. Modular production systems are becoming a fundamental aspect of manufacturing, providing a competitive advantage by increasing flexibility, reducing costs and enabling customization with ease.
Conclusion
The fourth industrial revolution, popularly known as Industry 4.0, signifies the confluence of advanced technologies like AI, IoT, and big data. However, it's not confined to transforming manufacturing and production processes. The customer service industry, too, has seen a paradigm shift, moving towards more proactive, efficient, and customer-centric models, thus evolving into Service 4.0.
By embracing these innovative strategies, businesses can enhance their service offerings, improve customer satisfaction, and stand out in an increasingly competitive landscape. As we progress further into the era of Industry 4.0, it becomes critical for businesses to adopt these advancements and adapt to the evolving needs of their customers.
For more insights into Industry 4.0 and its implications for customer service, explore our blog that provides a wealth of information on these topics and more.