Machine monitoring has established itself as a decisive factor for the efficiency and productivity of modern manufacturing processes. In the context of Industry 4.0 and the Industrial Internet of Things (IIoT), new opportunities are opening up for companies to monitor their machines in real time and thus minimize downtimes.

What is machine monitoring?
Machine monitoring refers to the continuous monitoring of machines and systems using sensors and software solutions. The aim is to record the condition of the machines in real time and detect potential problems at an early stage.
Advantages of real-time machine monitoring
- Increased efficiency: Continuous monitoring enables processes to be optimized and bottlenecks to be identified.
- Predictive maintenance: Prediction of maintenance requirements before faults occur.
- Cost reduction: Minimization of downtimes and extension of machine service life.
- Transparency: Clear insights into production processes and machine performance.
Technologies behind machine monitoring
The modern solutions are based on a combination of sensor technology, data analysis and networking:
- Sensors: Detect data such as temperature, vibrations or power consumption.
- IoT platforms: Network machines and enable data exchange.
- Big data and AI: Analyze large amounts of data and identify patterns for predictive maintenance.
Implementation of a machine monitoring solution
Step 1: Needs analysis
Identify which machines and processes should be monitored and which data is relevant. Contact our experts for an individual consultation.
Step 2: Select the right technology
Choose sensors and software solutions that fit your requirements. Pay attention to scalability and compatibility with existing systems. Our ADTANCE support solutions offer flexible options.
Step 3: Integration and training
Integrate the systems seamlessly into your production environment and train your staff to use the new technologies. Find out more about our training offers.
Case study: Successful implementation at a medium-sized company
A medium-sized company was able to reduce its downtimes by 30% by introducing real-time machine monitoring. By analyzing the sensor data, maintenance intervals were optimized and production processes were made more efficient.
The role of predictive maintenance
Predictive maintenance goes one step further than traditional machine monitoring. By predicting machine conditions, maintenance can be carried out exactly when it is needed, saving resources and increasing machine availability. Find out more about our predictive maintenance solutions.
Challenges and solutions
- Data management: The large amount of data requires effective analysis tools.
- Solution: Use of AI-supported analysis tools such as ADTANCE Smart Services.
- Security: Protection against cyber attacks is essential.
- Solution: Implementation of robust security protocols and regular updates.
- Costs: Initial investment can be high.
- Solution: Long-term planning and consideration of ROI through efficiency gains. Take advantage of our consulting services.
Future prospects
The development towards fully networked and intelligently controlled production environments will continue. Technologies such as machine learning and artificial intelligence will continue to revolutionize machine monitoring. Stay up to date with our blog.
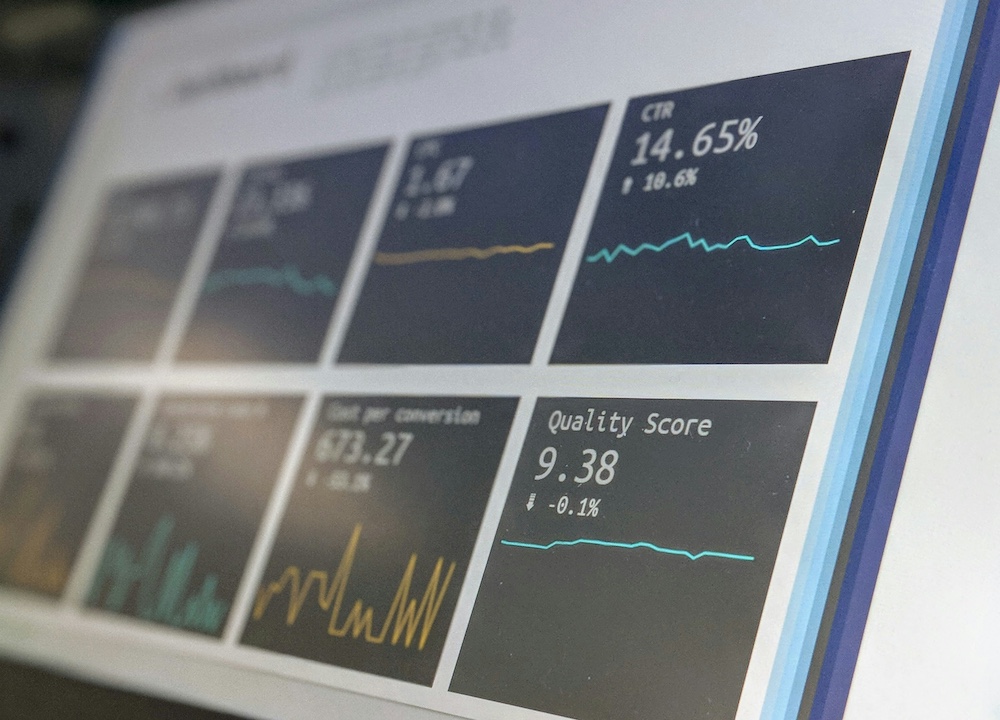
Conclusion
Machine monitoring is an indispensable part of modern production processes. It not only enables efficiency to be optimized, but also makes a significant contribution to cost reduction and quality assurance. Companies that invest in these technologies at an early stage secure competitive advantages and are ideally equipped for the future.
Interested in a customized machine monitoring solution for your company? Contact us and benefit from our expertise in the field of Industry 4.0 and IIoT.