Unexpected machine downtime can lead to significant production losses and costly delays. This can have serious financial implications, especially for small and medium-sized companies. However, with the use of technology and smart strategies, companies can take steps to prevent machine downtime.
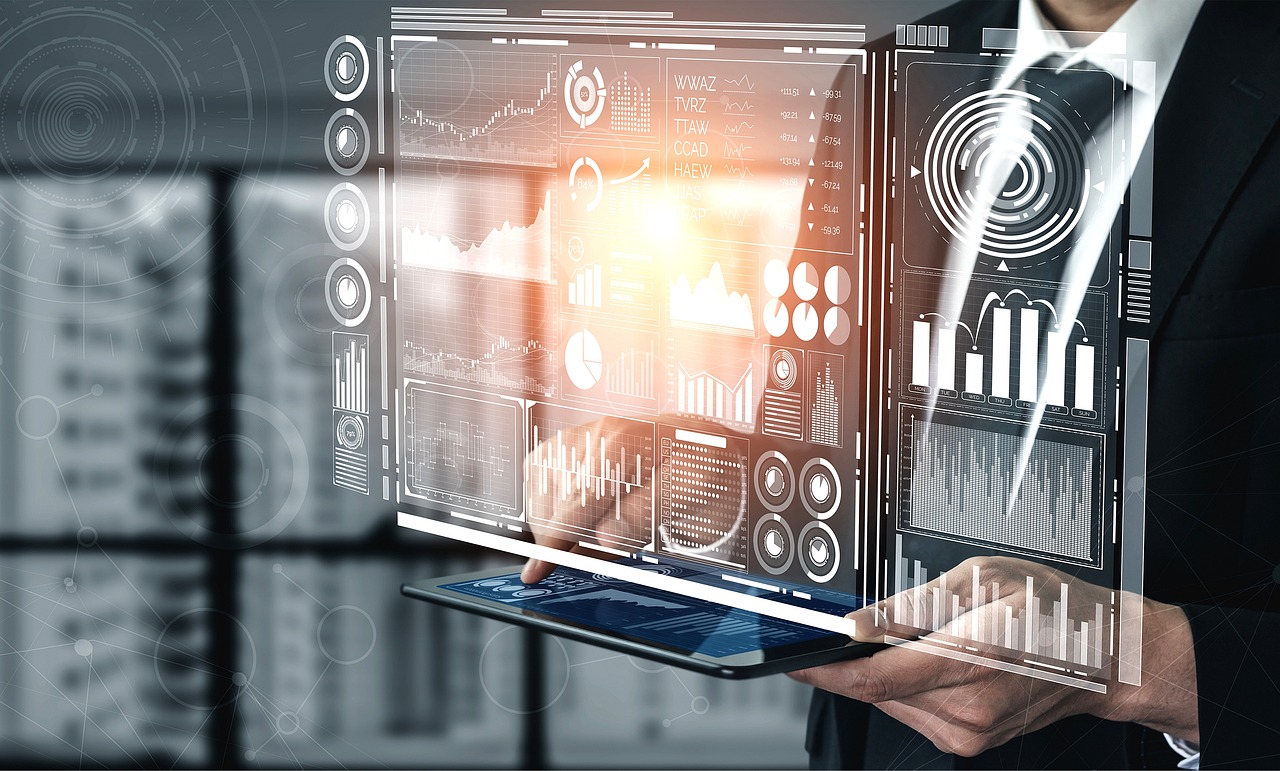
Understanding machine downtime
Before we focus on how to avoid machine downtime, it is important to first understand this phenomenon. A machine stoppage is an unplanned event in which a machine stops operating due to a fault or problem. This can be caused by mechanical failures, software problems, human error, or even external factors such as power outages.
Machine stoppages can have a serious impact on the production process, including lost production, increased labor costs, and possibly even damage to the machine itself.
The role of technology in preventing machine downtime.
In modern Industry 4.0, technology plays a critical role in preventing and managing machine downtime. By using innovative technologies such as predictive maintenance, IoT and Digital Twin, companies can monitor the condition of their machines in real time and identify potential problems before they lead to downtime.
Predictive Maintenance
One of the most effective tools for preventing machine downtime is predictive maintenance. By analyzing data from machines and equipment, companies can forecast and schedule maintenance work before a problem occurs. This approach can help minimize unplanned downtime and extend equipment life.
Industry 4.0 and IoT
Industry 4.0 and the Internet of Things (IoT) have revolutionized the way companies monitor and manage their production. By using IoT devices to collect data, companies can gather a wealth of information about their machinery and equipment. This data can then be analyzed to identify and fix potential problems before they lead to a shutdown.
Digital twin
Another key to avoiding machine downtime is the use of digital twins. A digital twin is a virtual copy of a physical machine or plant that allows operators to monitor and analyze its condition in real time. This can help identify potential problems and take preventive measures to avoid machine downtime.
Implementing effective strategies
In addition to using technology, it is also important to implement effective strategies to prevent machine downtime. This can include training personnel, improving maintenance practices and optimizing operations. For example, an effective asset management strategy can help track equipment condition and performance and reduce the likelihood of downtime.
Train staff
A well-trained workforce is one of the best lines of defense against machine downtime. Employees who know how to properly operate and maintain machinery can help prevent mistakes and identify potential problems early. Companies should invest in training and education for their employees to ensure they have the skills and knowledge they need to.
Improve maintenance practices.
Regular and thorough maintenance is critical to preventing machine downtime. Companies should ensure they have an effective maintenance plan and that all maintenance is properly documented. This can help identify potential problems early and take preventive action.
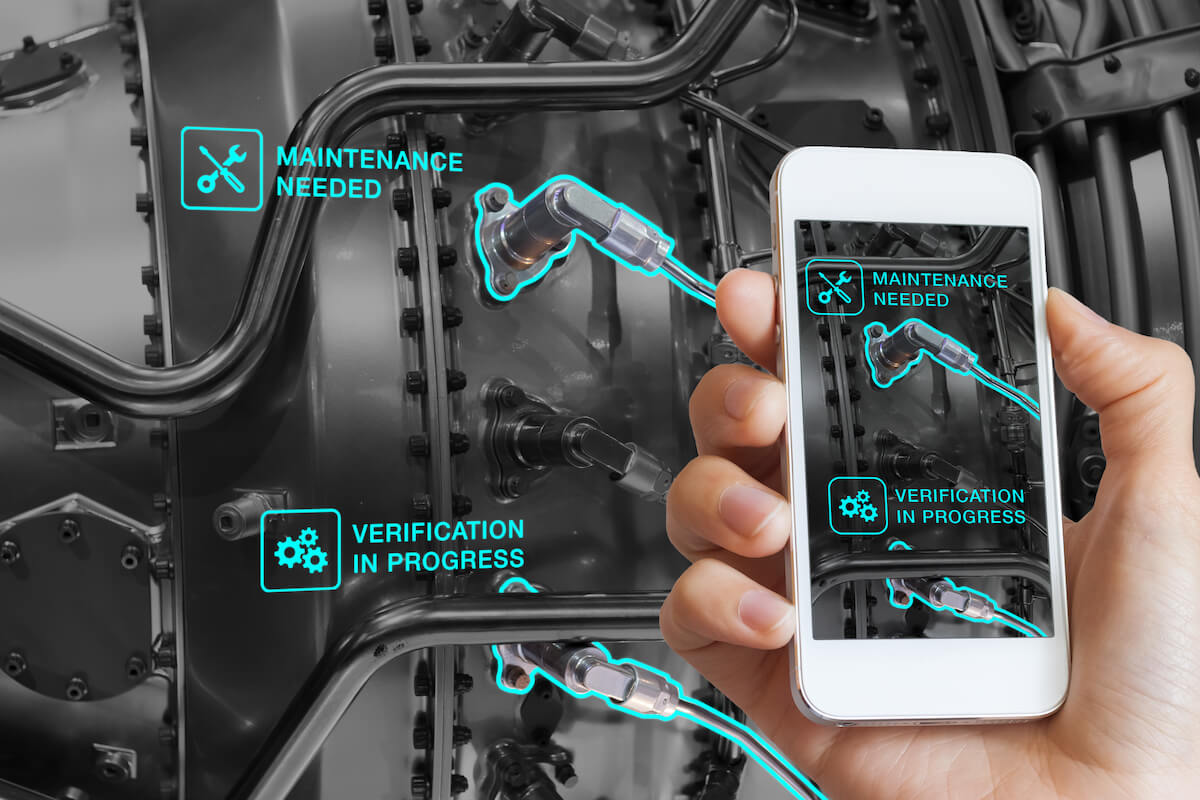
Optimizing operating processes
Optimizing operations can also help prevent machine downtime. This can include improving efficiency, reducing waste or improving quality. To do this, companies can use technologies such as workflow management systems to monitor and improve their processes.
Finally, it is important to remember that preventing machine downtime is an ongoing process. It requires constant monitoring, adjustment, and improvement to ensure that your machines and equipment are always running optimally. The good news is that with the right tools and strategies, machine downtime can be prevented and production efficiency increased.
Avoid machine downtime: The digital way to increase efficiency
Digital maintenance plans can also be of great importance in maintenance and repair to ensure that processes run smoothly. Such tools can provide on-site technicians with detailed instructions and checklists to identify and resolve potential malfunctions in a timely manner. It also allows access to documented expertise that would otherwise be difficult to obtain.
Another important point is asset management. Efficient management of operating resources and assets is essential to avoid machine breakdowns. A digital solution makes it possible to retrieve all relevant information in real time and to react better to changes or unexpected events.
Efficiency and reliability are the key words in modern mechanical engineering. With the right tools and technologies, companies can improve their service and significantly reduce machine downtime.
To make the most of the opportunities offered by digitization in customer service, it is important to link all available tools and technologies. This enables comprehensive service that is not only reactive, but also proactive. In the course of this, the topic of predictive maintenance is playing an increasingly important role. With the help of predictive maintenance, possible malfunctions and failures can be detected in advance before they lead to costly downtimes.
In this context, data glasses are often used to give on-site technicians a virtual view into the machine and assist in troubleshooting. At the same time, experts can be called in remotely to help find solutions. This Service 4.0 approach enables faster and more effective troubleshooting.
- The need for an efficient maintenance and repair strategy.
- the importance of asset management
- the advantage of predictive maintenance
- the role of data glasses and service 4.0
However, despite all the advances and new technologies, it remains a challenge to understand machine downtime and take appropriate measures to prevent it. A comprehensive understanding of the machine and its operation is critical. In this context, data analytics and artificial intelligence in manufacturing can also play a major role.
Artificial intelligence offers the potential to identify patterns and correlations that might remain hidden from the human eye. It also makes it possible to act with foresight and identify potential disruptions in advance. Together with modern ticketing systems in manufacturing, problems can be solved faster and downtime minimized.
The path to preventing machine downtime is one of continuous improvement and adaptation. It is important to use new technologies and methods to increase efficiency and improve customer service. But despite all the technology, the human factor must not be neglected. After all, it's the employees who deliver the service and use the technologies.
Concrete steps to avoid machine downtime with ADTANCE: Practical applications and strategies.
Now that we have discussed the basic aspects of digitization and how it can help prevent machine downtime, let's look at some concrete steps and strategies that can help minimize downtime.
1. Implement Predictive Maintenance.
With Predictive Maintenance, companies can identify potential problems before they lead to breakdowns. Continuous monitoring and analysis of machine data can identify patterns that could indicate future problems. Implement an effective predictive maintenance system and use artificial intelligence to make accurate predictions and prevent downtime.
2. Rely on remote service and assistance.
The ability to call in technicians and experts remotely can significantly speed up and improve the service process. By using data glasses and AR technology, specialists can take a virtual look inside the machine and provide valuable support. This enables faster and more efficient troubleshooting.
3. Invest in digital maintenance and repair plans.
digital maintenance plans and repair guides ensure that all necessary information and steps are available to perform efficient and effective maintenance or repair. With access to these resources, technicians can perform tasks correctly and quickly, reducing downtime.
4. Optimize your Asset Management
A efficient management and monitoring of your assets is crucial to ensure the smooth operation of your equipment. Digital asset management solutions allow you to access all relevant information in real time and react quickly to changes or unexpected events.
5. train your staff
The success of your machine downtime prevention strategy depends on your staff. Make sure your staff is adequately trained and has the necessary knowledge and skills to effectively use your technologies and tools.
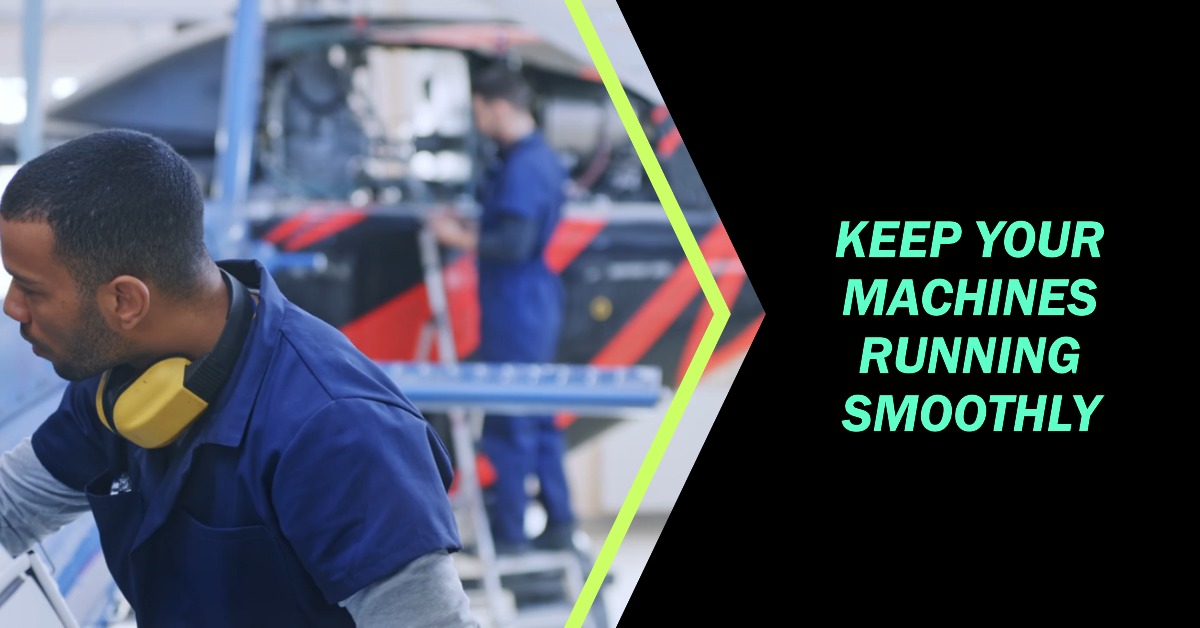
In the ever-evolving world of Industry 4.0, it's important to stay on the ball and constantly look for new ways to increase efficiency and improve operational performance. With the right technologies, strategies and a well-trained team, you can minimize downtime, reduce operating costs and improve customer service.
Digitization offers tremendous opportunities for businesses. But to take full advantage of these opportunities, it's important to take a strategic approach and use the right tools and technologies. It's an ongoing process that requires both commitment and a willingness to learn and adapt.
With the right partners on your side, like ADTANCE, you can successfully navigate digital transformation and take your business to the next level. Take the first step and discover how ADTANCE can help you avoid machine downtime and future-proof your business.