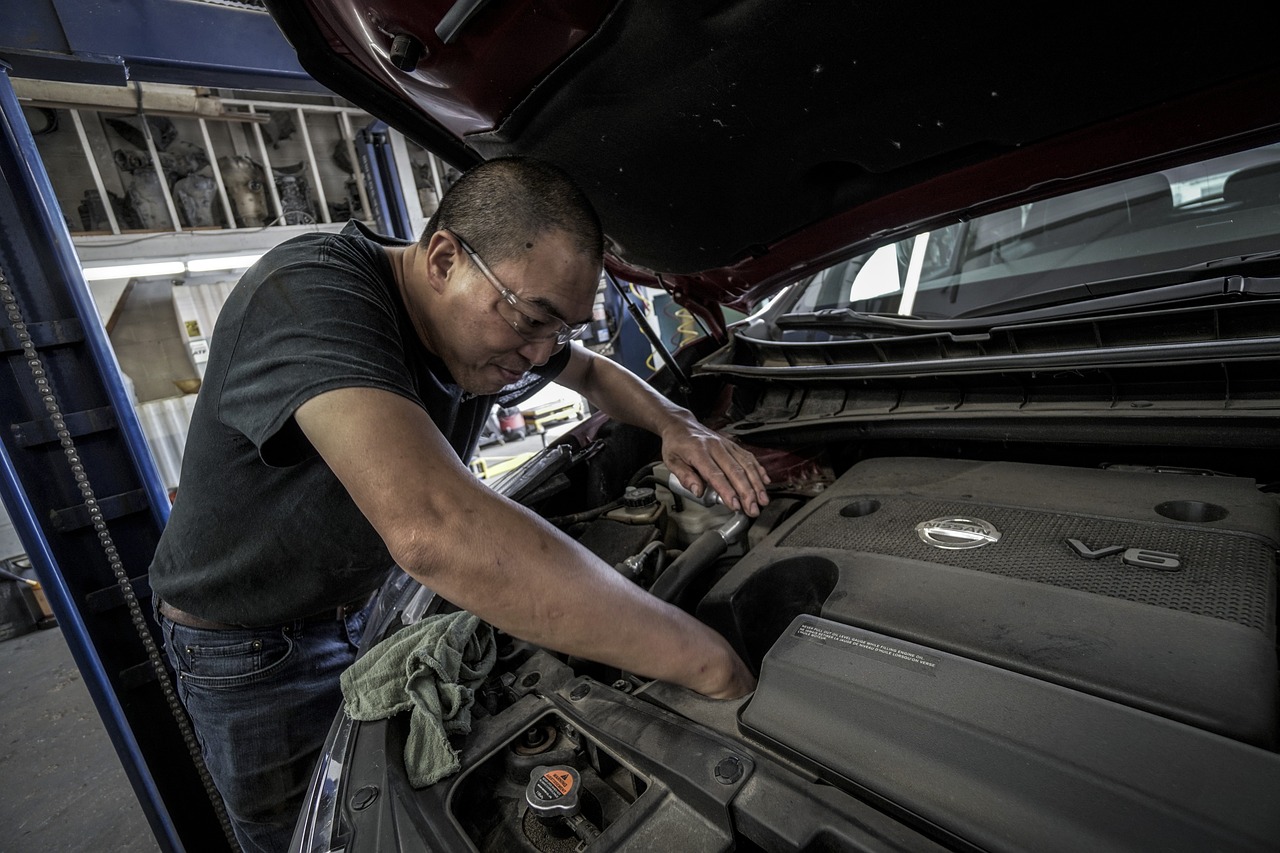
Introduction
Digital maintenance plans have revolutionized the way businesses manage and maintain their assets in today's technologically driven world. With the increasing complexity of equipment and systems, organizations are recognizing the need for more efficient and proactive approaches to maintenance. In this article, we will explore the concept of digital maintenance plans, their significance, and the benefits they offer in optimizing asset performance and reducing downtime.
Understanding Digital Maintenance
Digital maintenance entails the use of advanced technologies and data-driven strategies to monitor, analyze, and optimize maintenance activities. It goes beyond traditional preventive and reactive maintenance by leveraging real-time data, predictive analytics, and automation. A digital maintenance plan encompasses a comprehensive framework that integrates technology, processes, and people to ensure efficient asset management.
Key components of a digital maintenance plan include condition monitoring, asset performance management, data analytics, and maintenance scheduling. By collecting and analyzing data from various sources such as sensors, Internet of Things (IoT) devices, and equipment monitoring systems, organizations gain valuable insights into asset health, performance trends, and potential failure risks.
Implementing a Digital Maintenance Plan
Creating a digital maintenance plan involves several steps. Firstly, organizations need to assess their current maintenance practices and identify areas where digitization can bring significant improvements. This includes evaluating existing systems, data collection methods, and maintenance workflows. By understanding the gaps and opportunities, businesses can develop a roadmap for digital transformation.
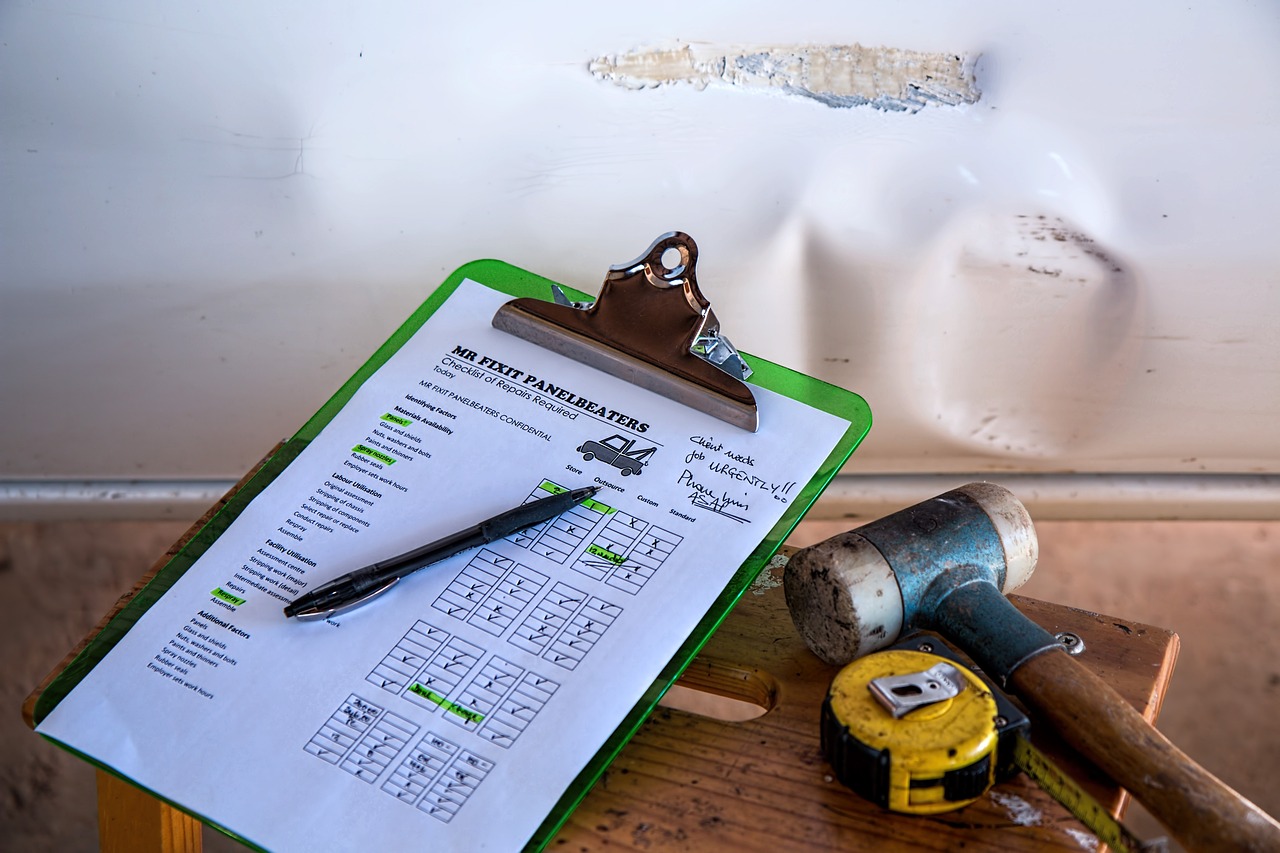
Next, selecting the right tools and technologies is crucial for successful implementation. This may include a combination of sensor networks, asset management software, cloud-based platforms, and predictive analytics solutions. Integrating these technologies allows for seamless data collection, analysis, and visualization, enabling timely decision-making and proactive maintenance interventions.
However, implementing a digital maintenance plan comes with its own set of challenges. Organizations must consider factors such as data security, system compatibility, and the need for skilled personnel. Adequate training and change management processes should be in place to ensure a smooth transition and acceptance of the new digital practices across the organization.
Key Features of an Effective Digital Maintenance Plan
An effective digital maintenance plan incorporates various features that enable proactive maintenance and optimize asset performance. Predictive maintenance techniques play a crucial role in identifying and addressing potential equipment failures before they occur. By leveraging historical and real-time data, organizations can predict maintenance needs, schedule interventions at the optimal time, and avoid costly unplanned downtime.
Real-time monitoring and data analytics form another vital component of digital maintenance plans. Continuous monitoring of equipment performance allows for early detection of anomalies, deviations, or signs of impending failures. Advanced analytics techniques, such as machine learning algorithms, enable organizations to derive valuable insights from the collected data, facilitating data-driven decision-making and proactive maintenance strategies.
Furthermore, integrating digital maintenance plans with IoT devices and sensors enables organizations to create a connected ecosystem of assets. Real-time data from these devices can be used to monitor asset health, track performance metrics, and trigger maintenance activities based on predefined thresholds. This integration fosters a proactive approach to maintenance, reducing the risk of unexpected breakdowns and maximizing equipment uptime.
Benefits of Digital Maintenance Plans
Digital maintenance plans offer numerous benefits to organizations across various industries. Firstly, they enhance equipment uptime and reliability. By identifying potential failures in advance, organizations can schedule maintenance activities during planned downtime, minimizing the impact on operations and reducing the risk of costly breakdowns.
Secondly, digital maintenance plans contribute to cost savings and improved efficiency. Proactive maintenance interventions based on data-driven insights help optimize maintenance schedules, reduce the need for reactive repairs, and optimize spare parts inventory. This results in reduced maintenance costs, increased asset lifespan, and improved overall operational efficiency.
Moreover, digital maintenance plans enhance safety and risk management. By continuously monitoring equipment performance and addressing maintenance needs promptly, organizations can mitigate safety risks associated with faulty or poorly maintained assets. This ensures a safer working environment for employees, reduces the likelihood of accidents, and minimizes potential liabilities.
Case Studies: Successful Implementation of Digital Maintenance Plans
Several companies have successfully implemented digital maintenance plans, yielding significant benefits. For example, a manufacturing company integrated IoT sensors into their production equipment, enabling real-time monitoring of critical parameters. This allowed them to detect anomalies early, predict maintenance needs, and optimize equipment performance, resulting in a 30% reduction in downtime and a 20% decrease in maintenance costs.
Similarly, a utility provider implemented a predictive maintenance system that analyzed data from their electrical grid infrastructure. By identifying potential failures in transformers and power lines, they were able to schedule proactive maintenance, reducing unplanned outages by 40% and improving customer satisfaction.
These case studies demonstrate the positive impact of digital maintenance plans on operational efficiency, cost reduction, and customer satisfaction.
Future Trends in Digital Maintenance
The field of digital maintenance is continuously evolving, with several future trends shaping its trajectory. Advancements in artificial intelligence and machine learning algorithms are expected to play a significant role in automating maintenance activities, enabling better prediction accuracy, and optimizing resource allocation.
Digital twins, virtual replicas of physical assets, are gaining popularity in maintenance planning. By creating digital representations of equipment and systems, organizations can simulate different scenarios, conduct virtual testing, and optimize maintenance strategies without impacting actual operations. This technology has the potential to revolutionize the way maintenance is planned and executed.
Additionally, emerging technologies such as augmented reality (AR) and virtual reality (VR) are being explored for their potential in maintenance training, troubleshooting, and remote assistance. These immersive technologies can enhance the skills of maintenance personnel, improve equipment diagnostics, and enable remote collaboration with experts.
Conclusion
Digital maintenance plans have emerged as powerful tools for organizations to optimize their asset management and maintenance practices. By harnessing the potential of technology, data analytics, and predictive techniques, businesses can achieve higher equipment reliability, reduced downtime, and improved operational efficiency. Embracing digital maintenance plans is essential for staying competitive in today's rapidly evolving business landscape.
Contact us or schedule an appointment for more insights on how we can help you optimize your digital maintenance.
FAQ
-
What is a digital maintenance plan?
A digital maintenance plan utilizes advanced technologies and data-driven strategies to monitor, analyze, and optimize maintenance activities. It integrates technology, processes, and people to ensure efficient asset management. Key components include condition monitoring, asset performance management, data analytics, and maintenance scheduling. -
How is a digital maintenance plan implemented?
Implementation involves assessing current maintenance practices, identifying areas for improvement, and developing a roadmap for digital transformation. Selecting the right tools and technologies is crucial, which may include sensor networks, asset management software, cloud-based platforms, and predictive analytics solutions. Challenges such as data security, system compatibility, and the need for skilled personnel must also be considered. -
What are the benefits of digital maintenance plans?
Digital maintenance plans enhance equipment uptime and reliability, contribute to cost savings and improved efficiency, and enhance safety and risk management. By identifying potential failures in advance, maintenance activities can be scheduled during planned downtime, reducing the risk of costly breakdowns. Proactive maintenance interventions based on data-driven insights help optimize maintenance schedules, reduce the need for reactive repairs, and optimize spare parts inventory. -
What are some successful implementations of digital maintenance plans?
Several companies have successfully implemented digital maintenance plans. For example, a manufacturing company integrated IoT sensors into their production equipment, enabling real-time monitoring of critical parameters. This resulted in a 30% reduction in downtime and a 20% decrease in maintenance costs. A utility provider implemented a predictive maintenance system that reduced unplanned outages by 40% and improved customer satisfaction. -
What are the future trends in digital maintenance?
Future trends include advancements in artificial intelligence and machine learning algorithms for automating maintenance activities, the use of digital twins for maintenance planning, and the exploration of augmented reality (AR) and virtual reality (VR) for maintenance training, troubleshooting, and remote assistance.