Quality assurance is a crucial aspect of modern industry, as it ensures that products and services meet the high standards that customers expect. As digitalization progresses, there are always new opportunities to make quality assurance processes more efficient and reliable. In this article, we present five simple quality assurance processes that you can digitize in 2024 to optimize your processes and minimize sources of error. These processes can be digitized using modern no-code applications that make it possible to checklists, step-by-step instructions and more without programming knowledge.
1. Inspection and maintenance logs
Description
Inspections-and-maintenance are essential components of quality assurance, especially in industries such as manufacturing, construction and automotive. Traditionally, these records have been kept on paper, leading to inefficient administration and an increased risk of errors.
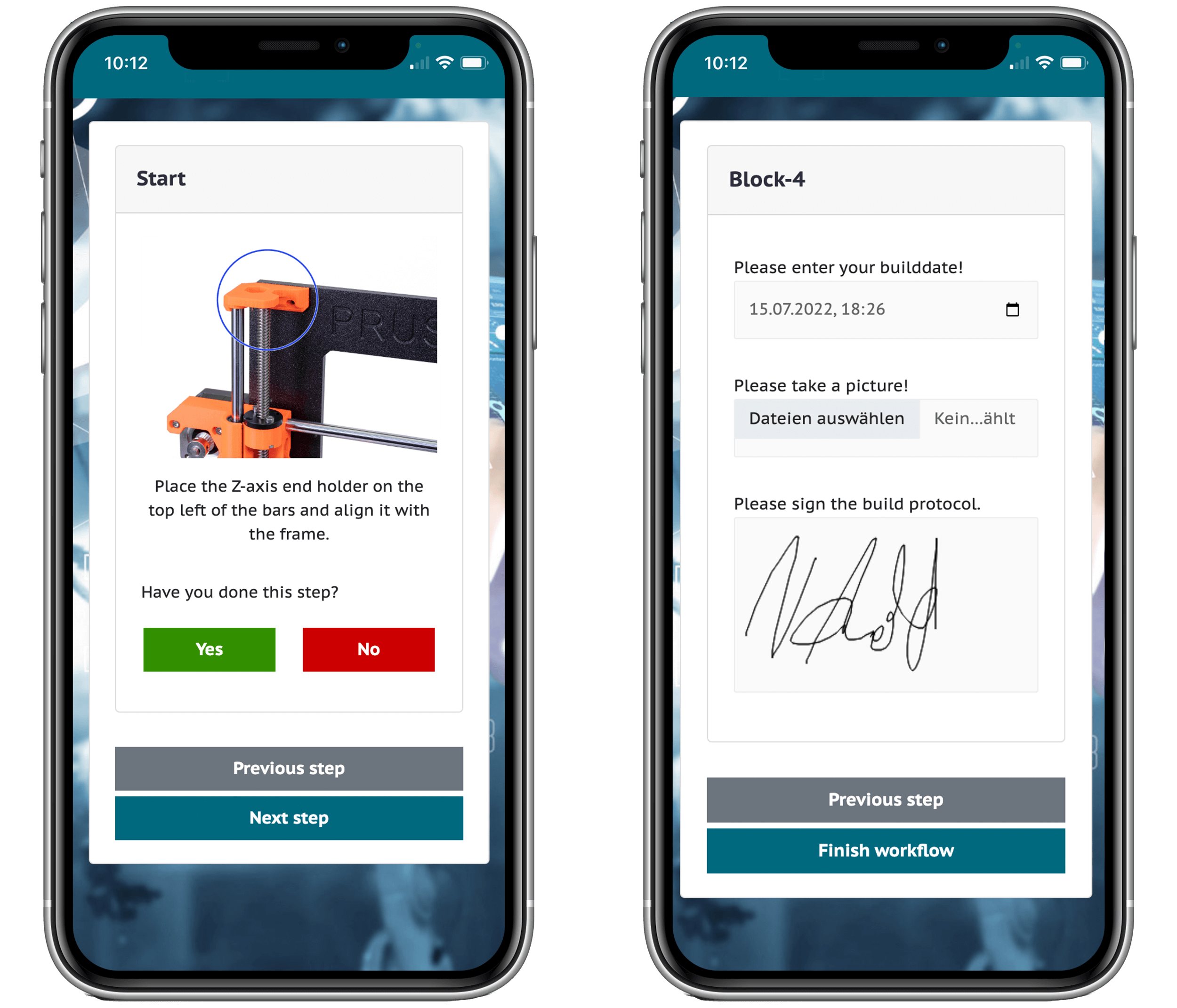
Digitization approach
Through the digitization of inspection and maintenance logs, companies can significantly improve the accuracy and efficiency of these processes. With a no-code application, you can create customized checklists and forms that are accessible on mobile devices. This allows inspectors to record their reports directly on site and immediately transfer them to a centralized system.
Benefits
- Real-time data access: Immediate availability of inspection data for all relevant departments.
- Error minimization: Reduction of human error through standardized digital checklists.
- Time saving: Faster execution and evaluation of inspections and maintenance.
2. Supplier evaluation
Description
Supplier evaluation and selection is a critical process to ensure that the materials and services a company receives meet quality standards. Traditionally, this evaluation is often done manually and is time-consuming.
Digitization approach
A digital supplier assessment enables continuous monitoring and evaluation of supplier performance. By creating digital evaluation forms, all relevant criteria such as delivery times, quality of delivered goods and service performance can be systematically recorded and evaluated.
Benefits
- Transparency: Clear and comprehensible evaluation processes.
- Continuous improvement: Identification of weak points and potential for improvement at suppliers.
- Efficiency: Faster and more precise evaluation and selection of suppliers.
3. Quality audits
Description
Quality audits are internal or external checks to ensure compliance with quality standards. These audits often include extensive documentation and reports that are created and processed manually.
Digitization approach
By using digital tools for quality audits, you can create standardized audit checklists and report formats. These digital forms can be used on mobile devices so that auditors can record their observations and results directly on site and transmit them in real time to the central system.
Benefits
- Standardization: Standardized and consistent audit procedures.
- Time saving: Faster execution and documentation of audits.
- Traceability: Seamless documentation of all audit processes and results.
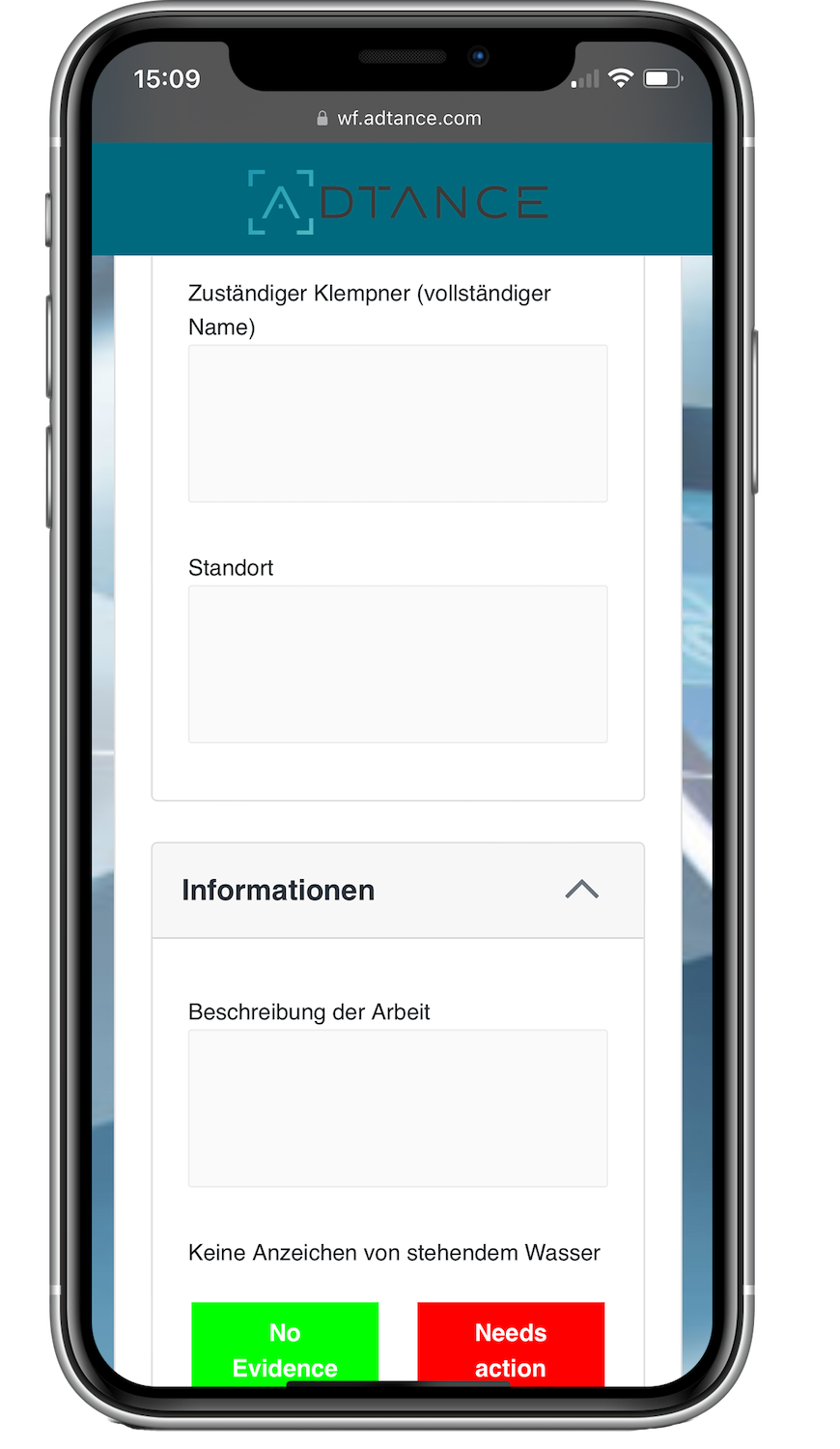
4. Employee qualification certificates
Description
The employee qualification and training is crucial to ensure high quality standards. Traditionally, training records and certificates are often managed in paper form or in various non-networked systems.
Digitization approach
By digitizing employee credentials, you can centrally manage all training and certification data. Using a no-code application, you can create and manage training plans, certification requirements and progress reports digitally.
Benefits
- Centralization: All qualification certificates in one place.
- Transparency: Easy access to employee qualification status.
- Efficiency: Automatic notifications about upcoming trainings or expiring certificates.
5. Complaint management
Description
The management of Customer complaints is an essential part of quality assurance. Traditionally, complaints are often received by phone or email and documented manually, which can lead to inefficient processing and tracking.
Digitization approach
By digitizing complaint management, you can implement a systematic and transparent process for recording, processing and tracking customer complaints. Digital forms and workflows make it possible to record all relevant information in a structured manner and track the processing status in real time.
Benefits
- Transparency: Clear tracking of the status of each complaint.
- Efficiency: Faster processing of complaints through structured workflows.
- Customer satisfaction: Improved customer satisfaction through swift and transparent processing of complaints.
Conclusion
The digitalization of quality assurance processes offers numerous benefits, including increased efficiency, reduced error rates and improved transparency. With modern no-code applications, companies can digitize these processes quickly and easily without the need for extensive IT resources. The five processes described - inspection and maintenance records, supplier evaluation, quality audits, employee qualification records and complaint management - are ideal candidates for digitization in 2024. By implementing digital solutions, companies can optimize their quality assurance processes and secure a competitive advantage.
Contact us to learn more about how ADTANCE Workflow can support you in your digitalization project.