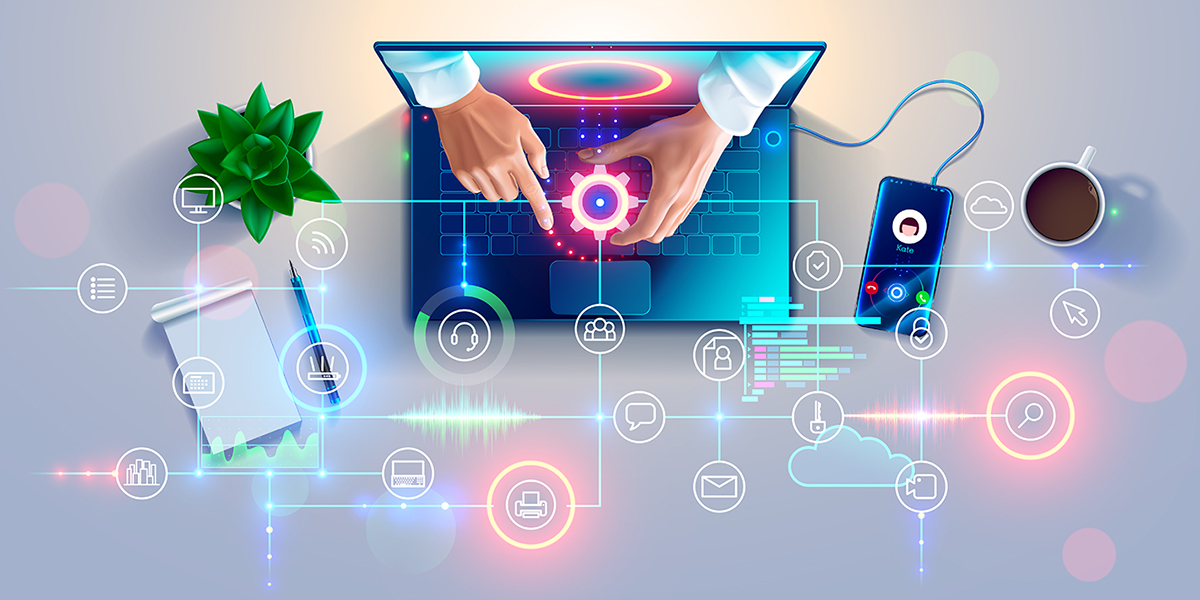
What is Remote Maintenance?
Remote maintenance, also called Remote Service, Remote Support or Remote Assistance, is well known from IT support. When a problem with a computer occurs, an IT expert who is not in the same office and perhaps not even in the same city can use software to access the computer and analyze the problem remotely and in the best case solve it directly.
Support when it is Needed
But such support is not only possible for software problems on a computer. For example, manufacturers of plants and machines also cover service cases and system maintenance via remote service by a customer service specialist. The expert can not only access the software of the system or machine. Via a video live stream, which is started on site by a system operator, the expert can also take a direct look at the systems and machines, detect problems and instruct the system operator to carry out maintenance or repairs by means of real-time transmission using data glasses or other end devices. The expert knows the plant and thus the areas that require special attention. By being able to see how the plant is behaving, he can give clear and individualized instructions to the worker in the field to quickly correct a fault.
Reasons for the Use of Remote Maintenance Systems
Optimization of the After Sales Service and Increase of Customer Loyalty
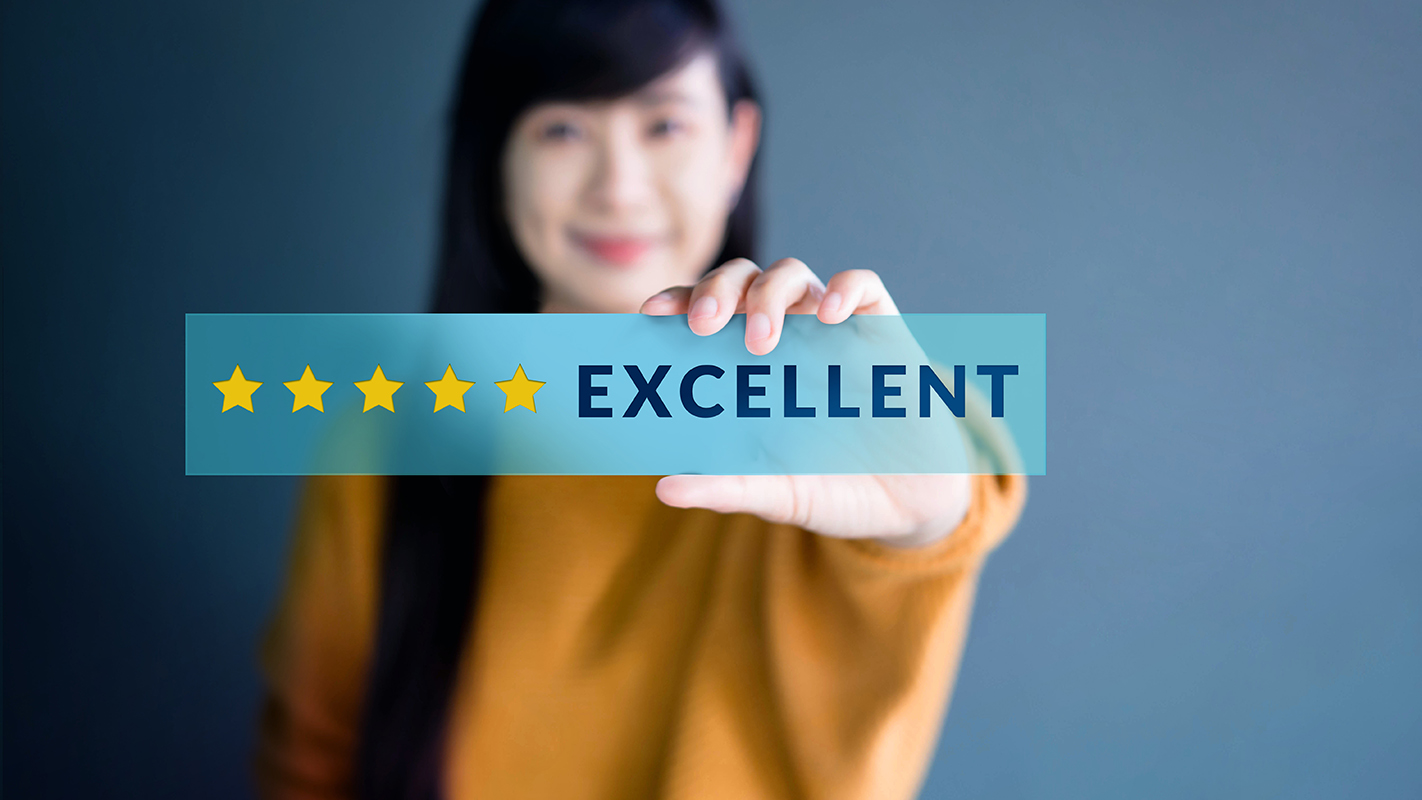
By integrating a remote maintenance system into the after-sales service, service availability for the customer is increased and customer service is optimized. By carrying out maintenance from the customer's own workplace, travel times for service experts are eliminated and the organizational effort required to coordinate the service operations is minimized. The service technicians can invest the saved time in other service cases. They can also respond as soon as a customer contacts them. The significantly faster response time increases customer satisfaction. The expert is immediately available and can support the customer directly without long travel times. Fast and flexible reaction times give the customer the assurance of optimal support through reliable customer service. And this not only for planned maintenance, but also in the event of malfunctions that need to be reacted to at short notice. A factor that significantly increases customer satisfaction. With the help of the system, the after-sales service expert can quickly gain an overview of the condition of the system and, through professional analysis and troubleshooting, eliminate the fault and increase system availability. The quick response time minimizes downtimes at the customer's site. The utilization of the machines is improved and production stops can be avoided in the best case.
The throughput time of service processes is measurably increased because the time saved means that considerably more requests can be responded to within one day. This improved availability of service performance results in improved adherence to delivery dates and ultimately promotes customer loyalty.
Cost Reduction Through Increased Efficiency
However, not only the time factor plays an important role in deciding on such a system. Another key point is the reduction of costs. By eliminating travel expenses and travel time, more cases can be processed because the expert no longer loses valuable working time in the car or plane. This gain in efficiency increases the margin.
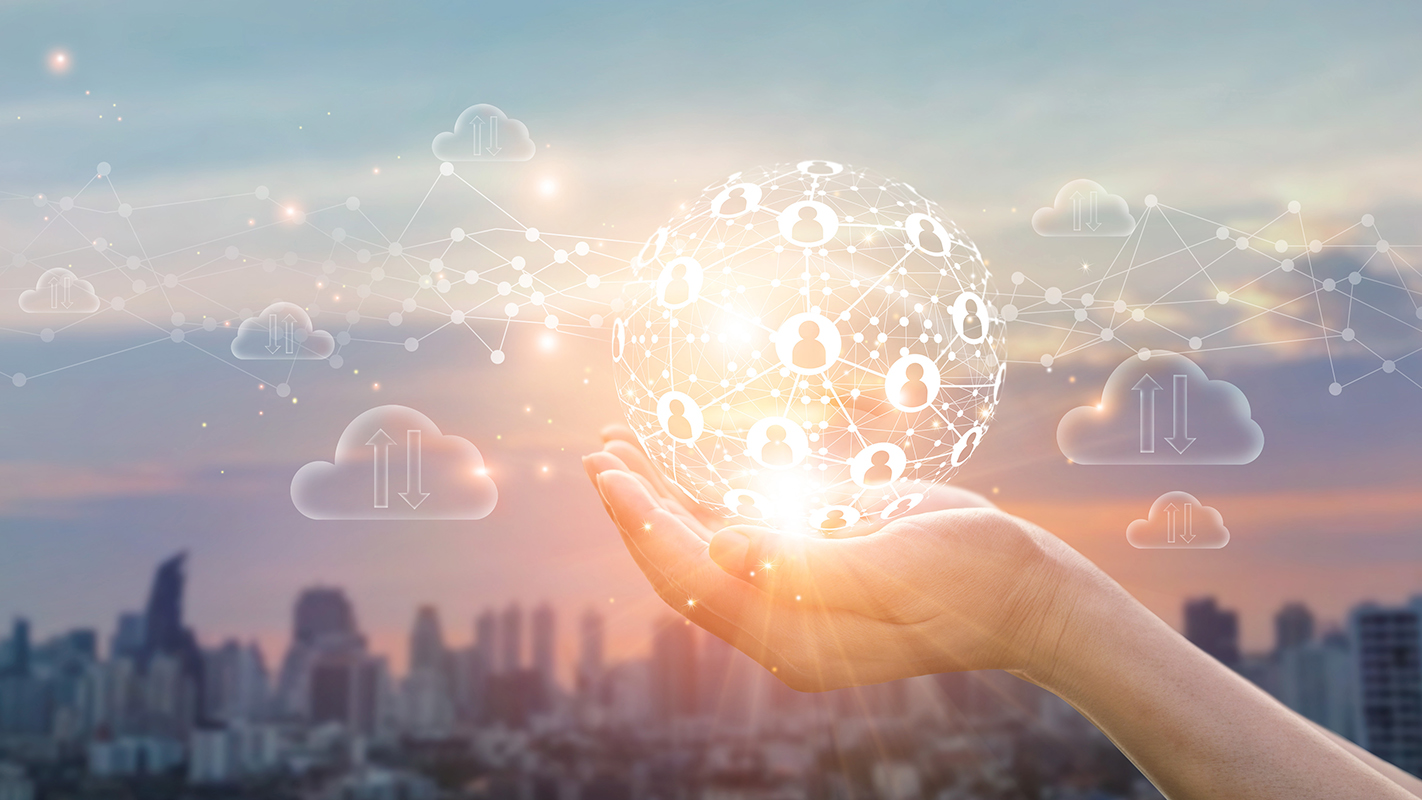
Extending your own service with the instrument of remote maintenance thus offers many advantages. But it is not only that the availability of the machines increases for customers due to less downtime and downtimes, and that system-related production losses and waiting times can be reduced. Due to the structured and documented problem solving of the experts with the help of the Videolivestream, recurring faults can be eliminated faster. The more remote maintenance and service calls are successfully solved and processed, the larger the data pool becomes, which can be accessed for future problems. This in turn improves the efficiency of the operation, because the time needed to analyze a problem and the way to solve it is shortened.
Thus equipped, the quality of the services can be maintained even with increasing speed in the processing of the assignments. The after sales service thus gains time that can be used for predictive maintenance. Since the manufacturer knows the maintenance cycles of the components he uses, maintenance can be offered as needed when the operating hours of the individual components are reached.
Supporting Customers Globally
Another reason for the introduction of Remote Service is the fact that customers can be serviced worldwide without additional effort. It no longer matters where an expert is needed. Even for international assignments, there is no longer a long lead time due to visa applications, travel planning or long travel times. The specialist is available at the same speed anywhere in the world.
Application Areas for Remote Maintenance
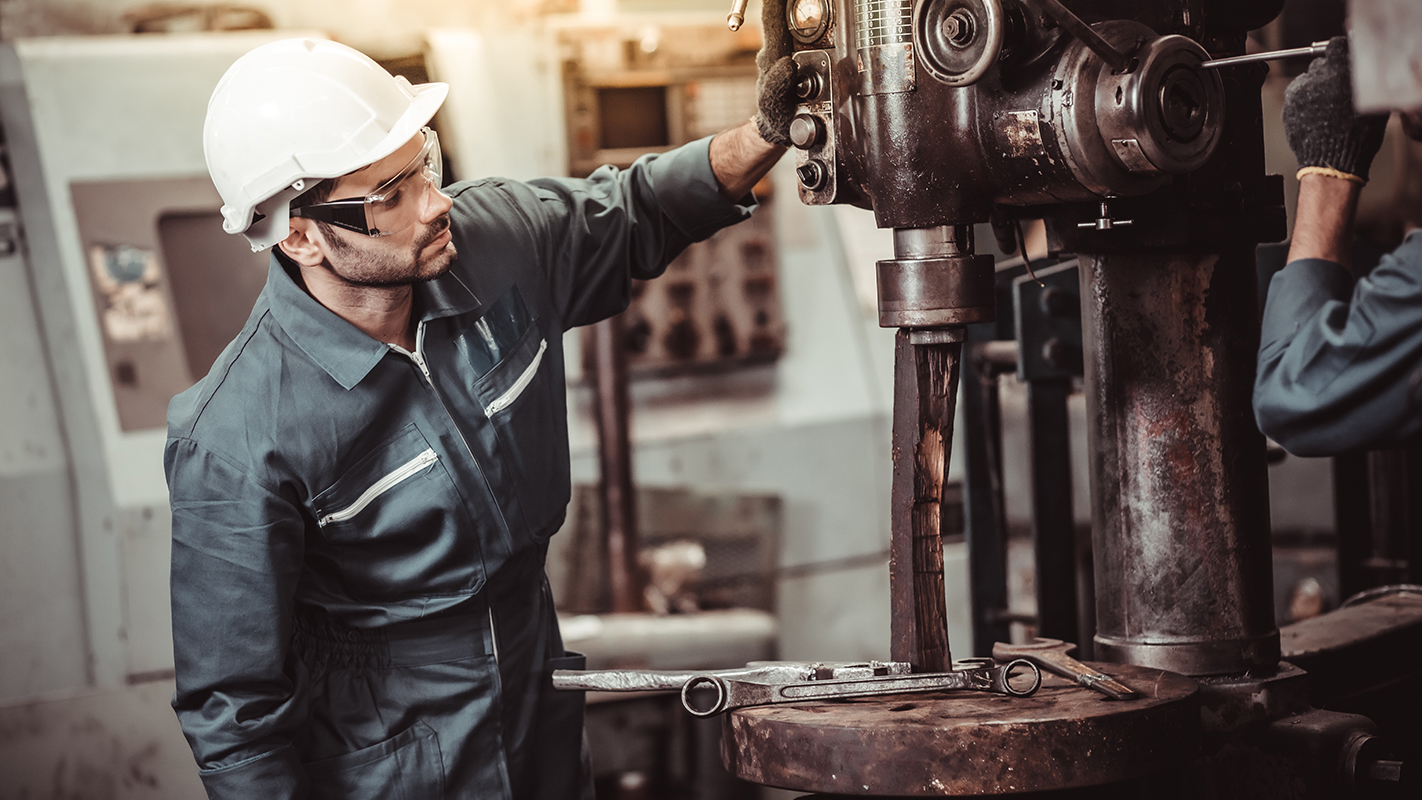
Remote maintenance finds its industrial application in plant and machine construction, in the automotive industry, in the chemical industry, in the packaging industry and in many other branches of industry.
A change in the production process, which makes minor modifications to a modular system necessary, optimizations in the process sequence, tests with raw materials and basic materials, which involve changes in process parameters, or the recommissioning of systems and machines - all this can be effectively implemented by video-supported remote maintenance.
Remote Maintenance in Plant and Machine Construction
Remote maintenance as a customer service is already widely used in plant and machine construction. With this system, customers can receive direct support from an expert of the manufacturer of the plants and machines.
The expert can examine the situation on site with the machine operators via video stream and with his expert knowledge he can instruct the worker on site to solve the problem. The worker at the machine has the comprehensive support to be able to eliminate a malfunction or to carry out the regular maintenance with exact specifications of the work steps to be carried out. He can exchange information with the expert, ask questions at any time and show and discuss specific conspicuous features of the system. Thus, the worker in the field has the certainty that each of his actions will be instructed and monitored and that he will be able to carry out repairs quickly and without loss of time.
Expand Expert Knowledge
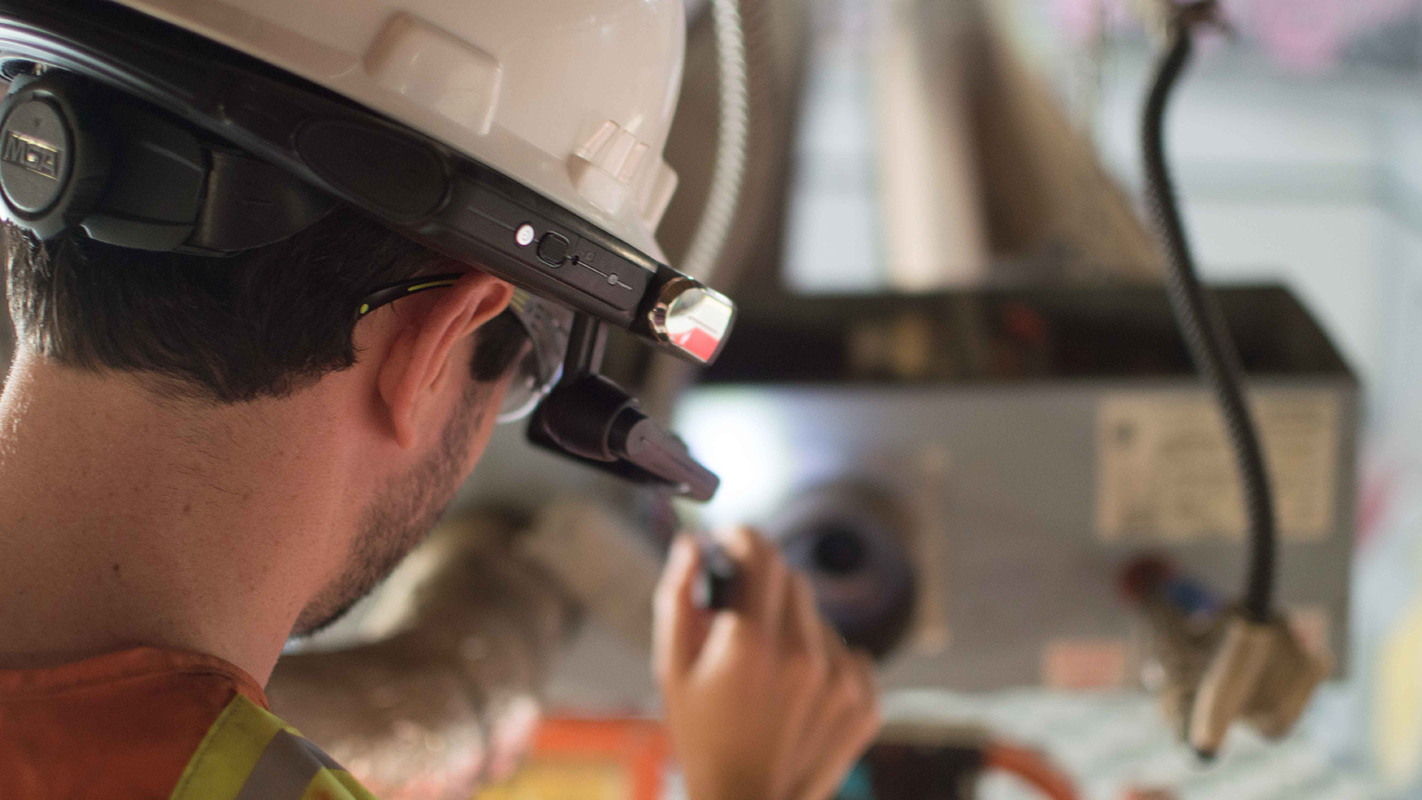
Subcontractors of a machine or a system can also be integrated to eliminate malfunctions. If a problem with a valve, a motor or a sensor occurs during commissioning or maintenance, the sub-supplier of the component can be integrated into the videolivestream, so that the expert knowledge can be broken down to each sub-component.
But not only in case of a sudden malfunction the advantage of using remote maintenance is shown. It is also used to supervise the installation of plants and machines and to support the commissioning on site afterwards. Furthermore, it is possible to approve components, such as safety valves, under the eyes of the customer, so that the customer no longer has to make a possibly long journey to the manufacturer. Training measures can also be carried out as after-sales service for customers or as support for the customer's own service experts with the Remote Support solution.
An Advantage for Everyone
By introducing a remote maintenance system, customers can be supported by specialists worldwide. This eliminates travel times and costs and increases the response time. Thanks to the prompt support, plant downtimes and production losses at customers can be minimized. This increases both customer loyalty and customer satisfaction.