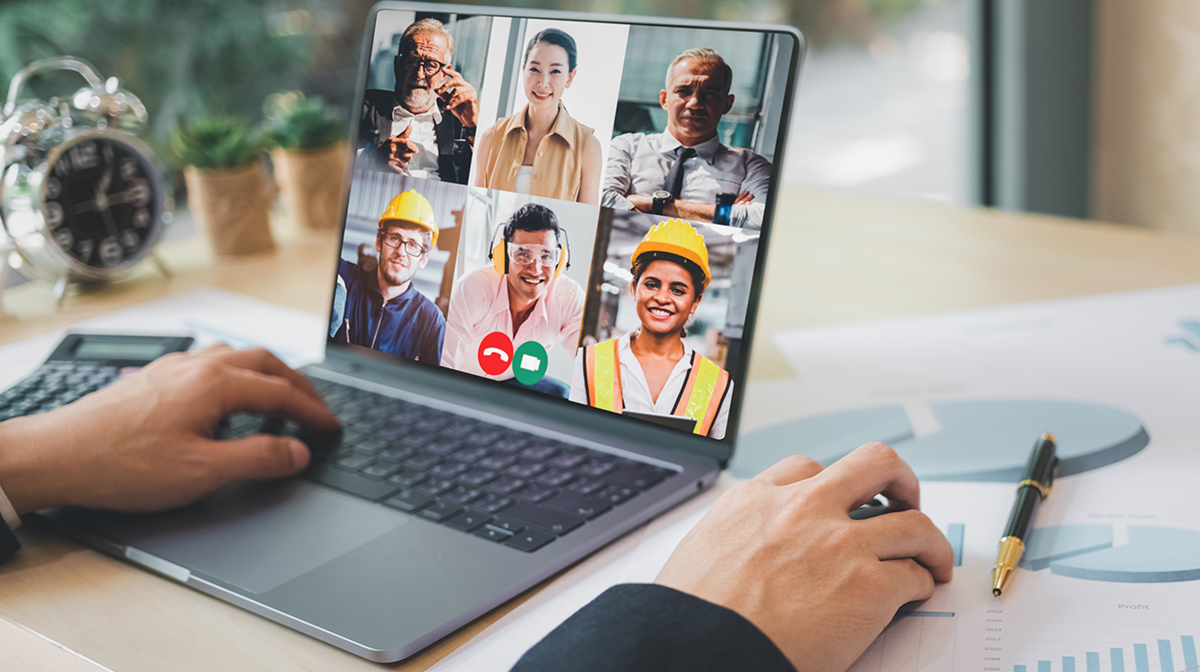
By now you're familiar with some of the benefits of implementing remote commissioning into your manufacturing and supply pipeline, and you understand how to measure its success. You're familiar with the savings you're likely to accrue from reducing your travel costs, and you expect to see greater production as a result of decreased machine downtime. There's another benefit of remote support that is often overlooked, namely the seamless integration of customer, supplier and third–party component suppliers to resolve a machine's malfunction. These component experts offer particular insight into machine parts that a service technician may be less familiar with, and can be incorporated into the resolution of any breakdown much more easily using remote support. To illustrate how third–party experts can become part of the team to improve customer service, we'll examine a scenario where our Smartglass technology has enabled component suppliers to join the troubleshooting process, how the capabilities of our remote support technology facilitated the resolution of the problem, and some extra advantages along the way.
Scenario
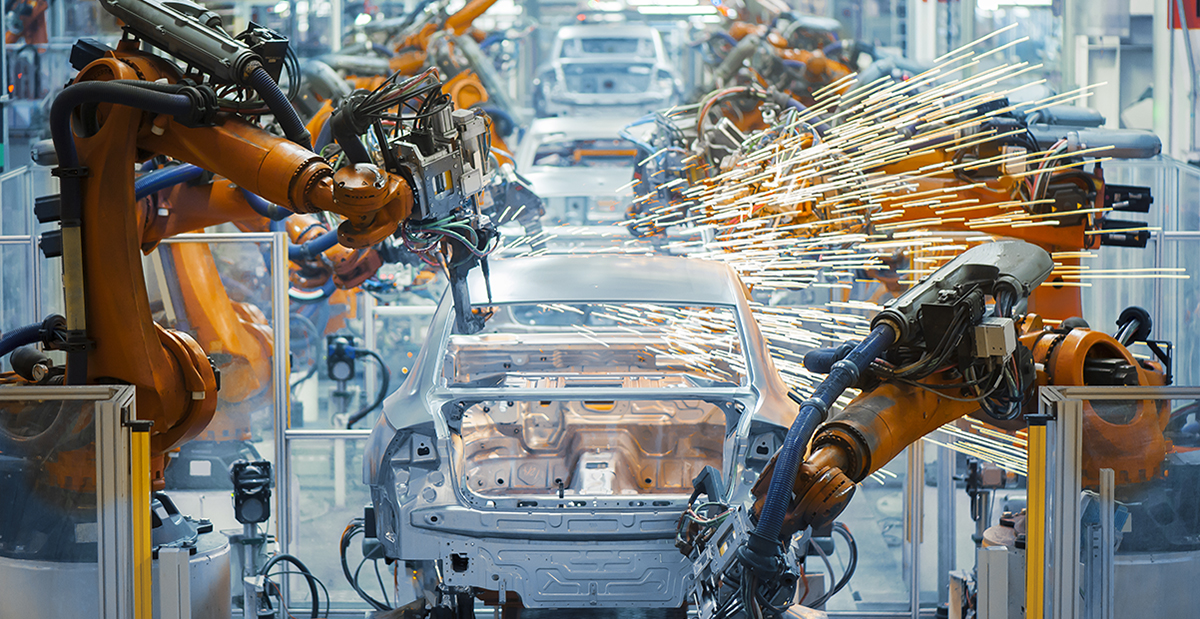
An automotive company uses robotic arms on its assembly line to produce engine parts, when one day a machine arm begins to overheat. After the arm and assembly line are shut down, the process of troubleshooting and repairs begins. The supplier of the damaged robotic arm has equipped the automotive company with Smartglasses and a remote support technology at the sale of their machine. To begin inspection of the damaged arm, a worker on the factory floor dons their data glasses, contacts the manufacturer, and begins a video live chat session with the manufacturer's service technician to begin examining the machine.
Thanks to the Smartglass, the supplier technician is given an over–the–shoulder view of the malfunctioning arm, and is able to guide the on–site worker through a series of steps to diagnose the issue. After thoroughly troubleshooting the arm, the technician determines that the problem lies with a damaged motor inside one of the actuators responsible for the arm's rotation. This particular component is not built in–house, but is supplied by a third–party manufacturer, so the technician's familiarity with it is limited. At this point, the benefits of remote support become especially clear. Normally, the third-party component supplier would need to travel to the facility site to repair the motor, after the service technician has already visited to inspect the arm. Instead, using remote support technology, the service technician invites an expert from the manufacturer of the damaged motor to join the troubleshooting session, and they quickly ascertain the source of the failure. As it turns out, the gearbox was in need of lubrication, as the motor had operated under a higher RPM than recommended—a problem that would have been detected if the automotive company had taken advantage of the predictive maintenance and continuous support features offered by the supplier as part of their remote commissioning. Now that the problem has been determined, the third–party motor supplier advises the floor worker on how best to lubricate the overheated gearbox, and prescribes a reduced operating load until the motor can be fully replaced. They proceed to order a new motor for installation, and the arm is restored to full functionality with minimal productivity disruption.
Capabilities
The above scenario is a realistic example of how remote support can integrate third–party component suppliers into a troubleshooting session to resolve machine malfunctions, but here are some specific capabilities of remote support technology that facilitate such collaboration.
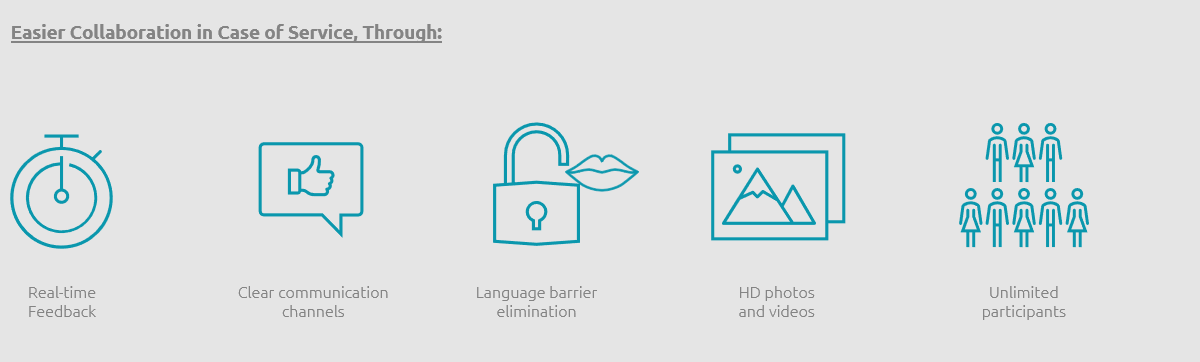
- Real–time feedback - Not only is the service technician able to see the machine from the on–site worker's view, but they are also able to export data such as machine schematics, blueprints, or diagrams to the data glasses' digital display. Technicians may even mark a specific point on the worker's field of vision to direct their attention where needed.
- Clear communication channels - The data glasses of our Partner RealWear for example are equipped with four noise–canceling microphones within the headset to enable clear communication between the on–site worker, service technician, and component supplier.
- Language barrier elimination - Oftentimes component suppliers may be located in different countries than the customer or manufacturing supplier, so language barriers can impede expedient machine repair. ADTANCE's remote support software isReal capable of translating 147 languages, enabling all parties to communicate clearly.
- HD photos and videos - The high–resolution video capacity of the Smartglasses enable users to take pictures of particular components, and also to stream their entire experience as they troubleshoot a machine. This allows them to watch the video later should the same problem occur again.
- Unlimited participants - A worker or service technician may invite as many colleagues or third–party component suppliers to the video live stream session as they wish, so all necessary parties may be involved.
By delivering such comprehensive information feedback and facilitating communication so clearly, remote support technology can effectively integrate multiple suppliers to resolve machine malfunctions, and ultimately improve customer service.
Design Specifications
In many cases, a remote support device with such robust data transmission capability would not withstand the typical operating conditions of a manufacturing floor, but this is not the case with data glasses. The primary application of the Smartglass is real–time maintenance, troubleshooting, and repair on a production site, so user–friendliness and durability are of paramount importance. The designers of Smartglass have engineered their data glasses with such ruggedness in mind. The specifications of the smartglasses are described below using the RelWear HMT -1 as an example:
- The adjustable micro–display sits close enough to the user's eye to be viewed as an equivalent 7-inch tablet size, and can be removed from sight when necessary.
- All functions of the Smartglass can be activated completely hands–free, freeing the user to perform repairs and inspections as needed.
- RealWears HMT-1 data glasses are fully integrable into all PPE equipment, so users may still don all hard hats, bump caps, or safety goggles necessary to perform all repairs while adhering to safety regulations.
- The 3.5 mm audio jack can be attached to any noise–canceling headphones the user is required to wear, so workers may still communicate with the service technician in loud environments.
- The Smartglass is designed to withstand a drop impact of up to 2 meters, operate in temperatures from -20 C to 50 C, and comes with a swappable battery for continuous operation, so it can endure for extended periods under the physically harsh conditions often found in a manufacturing setting.
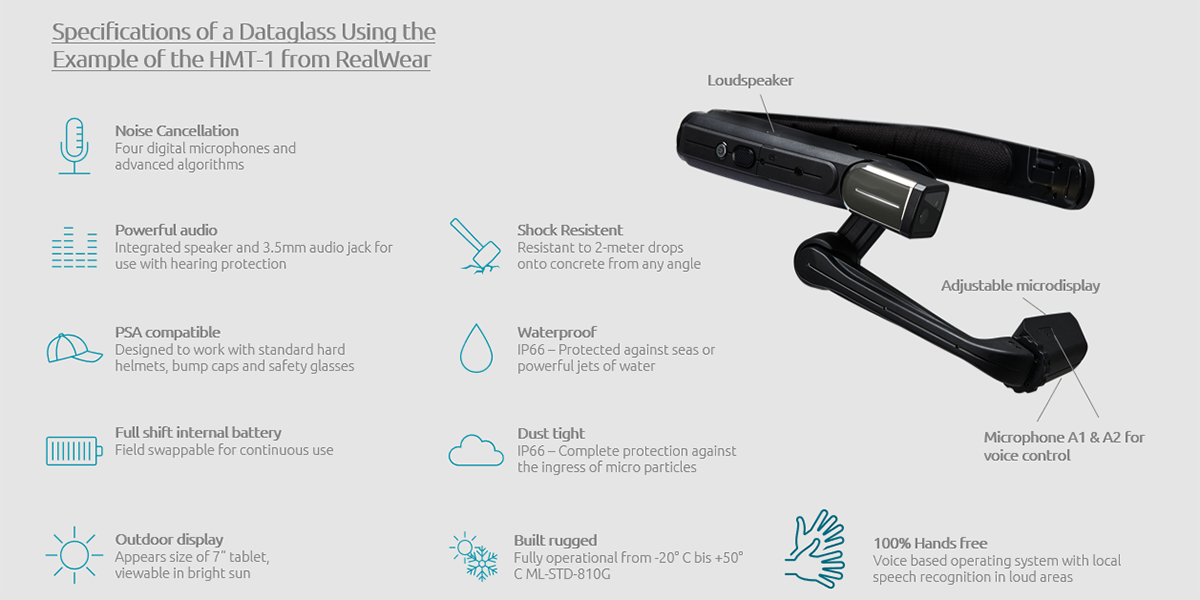
The rugged design of remote support hardware enables it to function amidst physically harsh operating conditions such as construction sites and factory floors, transmitting data and enabling collaboration where it's needed most.
Further Advantages
Facilitating communication amongst suppliers is a tremendous asset in expediting machine repairs, but there are multiple other advantages that come with such a team approach.
Reduced Delay
Without remote support, it is likely that in the above scenario, a service technician from the manufacturing supplier would have first had to travel to the customer's site, which in itself would have taken days of prolonged machine downtime. Not only does this adversely impact the customer's productivity and increase the supplier's travel costs as shown before, but once the service technician arrives and determines that he cannot solve the problem, another technician from the component supplier must be brought in, and the process repeats, costing even more in travel time for the supplier and machine downtime for the customer.
With remote support, all of these inefficiencies are circumvented. The manufacturing supplier technician not only can view the problem immediately to potentially resolve it, but if he is unable to do so, he may contact the component supplier at that moment, eliminating the need for service visits from either the manufacturing technician or component supplier.
Consultation
Should the manufacturer need to consult the third–party supplier regarding the operating conditions or design of their component, this process is made much easier by remote support as well. Instead of attempting to travel to the site and meet or overcome language barriers and miscommunications, both the manufacturer and component supplier may collaborate to understand their devices better—a process facilitated by the information and translation capabilities of the data glasses.
Customer Care
A customer who incurs all the costs associated with a machine malfunction is already going to be displeased; add to that the burden of having a service technician show up only to say that another visit from a third–party supplier is necessary—requiring more machine downtime and even greater cost—and the customer's frustration will be even greater.
By using remote support solutions, an organization may avoid any negative appearance from their customer as a result of a service technician being unfamiliar with a third–party supplier's component. Instead of telling the customer they have no solution, the technician may simply inform them that they are contacting a colleague on their behalf, allowing the customer to continue to feel that they are in good hands.
Overview
A machine malfunction that requires input from a third–party component supplier is an all too common occurrence, and can result in even longer repair delays and subsequently increased machine downtime—all of which impacts productivity and customer satisfaction. When manufacturing suppliers avail themselves of remote support technology such as Adtance's data glasses, component suppliers can be brought into the troubleshooting session to help on–site workers make any repairs in real–time, and get to the solution sooner. Adtance's Smartglasses possess both the digital innovation and rugged design to facilitate multi–party collaboration amidst the harsh operating conditions of a manufacturing setting, empowering suppliers to deliver the customer support that clients expect and optimizing machine performance as well. With such customer support improvements and productivity boosts available, it appears the solution for better collaboration is right in front of their eyes; Smartglasses are the answer.