Die Einführung eines Condition Monitoring Systems ist ein entscheidender Schritt für Unternehmen im Maschinen- und Anlagenbau, um die Effizienz ihrer Wartungsstrategien zu maximieren und Ausfallzeiten zu minimieren. Sie wissen, wie wichtig es ist, Maschinenverfügbarkeiten zu sichern und die Betriebskosten zu optimieren. Dieser Artikel bietet Ihnen eine detaillierte Anleitung in fünf Schritten zur erfolgreichen Implementierung einer Condition Monitoring Lösung, ohne dabei auf externe Sensoren einzugehen.
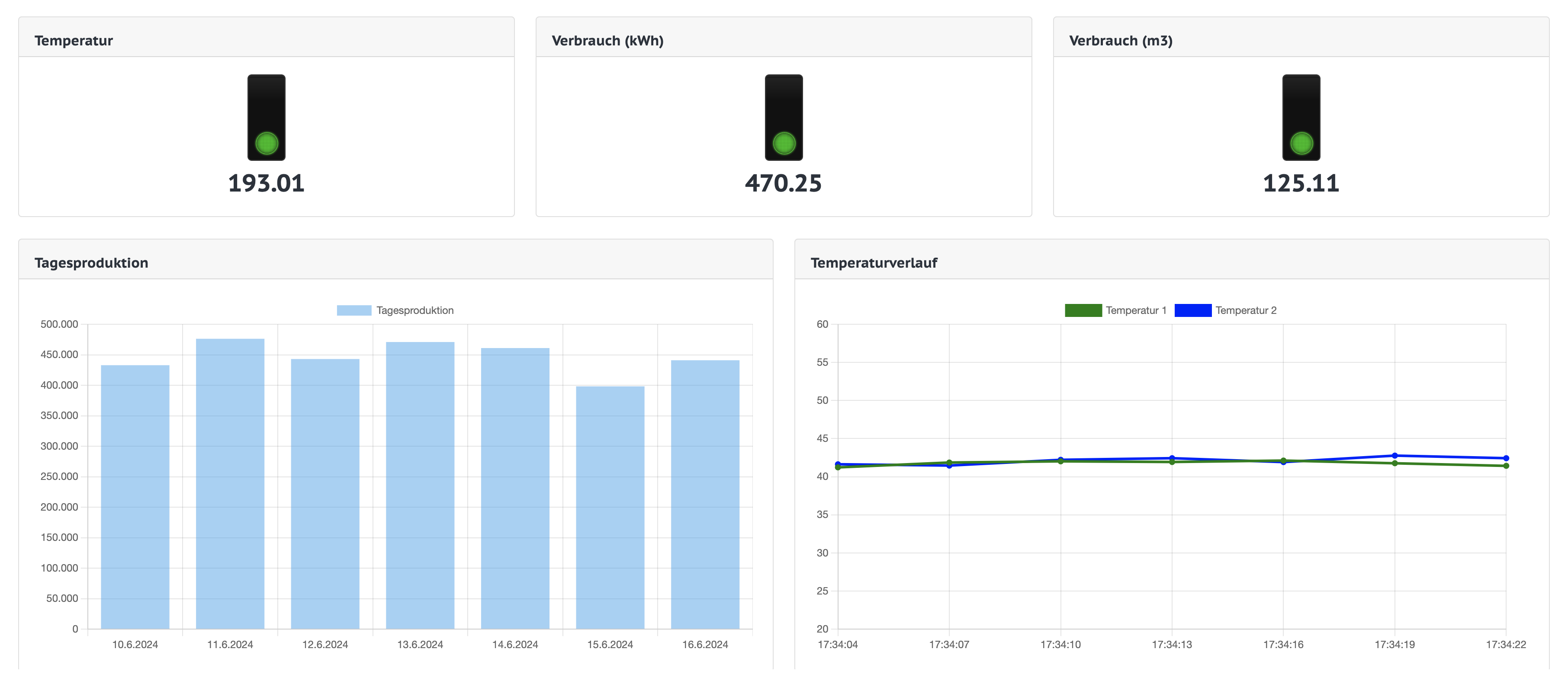
Schritt 1: Bestandsaufnahme und Zielsetzung
Bestandsaufnahme
Der erste Schritt zur Einführung eines Condition Monitoring Systems besteht darin, eine umfassende Bestandsaufnahme Ihrer bestehenden Maschinen und Anlagen durchzuführen. Dies umfasst:
-
Erfassung der Maschinen und Anlagen: Identifizieren Sie alle relevanten Maschinen und Anlagen in Ihrem Betrieb, die überwacht werden sollen. Erstellen Sie eine detaillierte Liste, die Informationen wie Hersteller, Modell, Baujahr, technische Spezifikationen und bisherige Wartungshistorie enthält.
-
Analyse des aktuellen Zustands: Dokumentieren Sie den aktuellen Zustand jeder Maschine. Dies kann durch Inspektionen, Wartungsberichte und vorhandene Betriebsdaten erfolgen. Ziel ist es, ein klares Bild des Ausgangszustands zu erhalten.
-
Ermittlung kritischer Maschinen: Bestimmen Sie, welche Maschinen für den Produktionsprozess am kritischsten sind. Diese Maschinen sollten im Fokus der Condition Monitoring Lösung stehen, da ihr Ausfall erhebliche Auswirkungen auf die Produktion haben kann.
Zielsetzung
Nachdem Sie eine gründliche Bestandsaufnahme durchgeführt haben, ist es wichtig, klare Ziele für das Condition Monitoring zu definieren:
-
Reduzierung ungeplanter Ausfälle: Ein Hauptziel könnte sein, die Anzahl ungeplanter Ausfälle zu minimieren, indem potenzielle Probleme frühzeitig erkannt werden.
-
Verlängerung der Maschinenlebensdauer: Durch kontinuierliches Monitoring und rechtzeitige Wartungsmaßnahmen kann die Lebensdauer der Maschinen verlängert werden.
-
Kosteneinsparungen: Langfristige Kosteneinsparungen durch reduzierte Wartungskosten und vermiedene Produktionsausfälle sind ebenfalls ein wichtiges Ziel.
-
Verbesserung der Wartungsplanung: Optimierung der Wartungsintervalle durch den Einsatz von Zustandsdaten, um präventive Wartungsmaßnahmen besser zu planen.
Schritt 2: Auswahl der geeigneten Monitoring-Methoden
Im nächsten Schritt müssen Sie die passenden Monitoring-Methoden auswählen, die für Ihre spezifischen Maschinen und Anlagen geeignet sind. Ohne auf externe Sensoren einzugehen, können folgende Methoden in Betracht gezogen werden:
Nutzung bestehender Datenquellen
-
Maschinendatenanalyse: Viele moderne Maschinen und Anlagen verfügen bereits über integrierte Datenquellen wie Steuerungssysteme und interne Sensoren. Diese Daten können genutzt werden, um den Zustand der Maschinen zu überwachen.
-
Historische Betriebsdaten: Analysieren Sie historische Betriebsdaten, um Muster und Trends zu identifizieren, die auf bevorstehende Probleme hinweisen könnten.
-
Wartungsberichte: Nutzen Sie vorhandene Wartungsberichte und Inspektionsdaten, um Anomalien und wiederkehrende Probleme zu identifizieren.
Methoden zur Datenanalyse
-
Vibrationanalyse: Analysieren Sie Vibrationen und Schwingungen, die von Maschinen erzeugt werden, um Abweichungen vom Normalzustand zu erkennen.
-
Thermografie: Überwachen Sie die Temperaturverteilung auf Maschinenoberflächen, um Hotspots und ungewöhnliche Erwärmungen zu identifizieren.
-
Akustische Analyse: Nutzen Sie Geräusche und Ultraschall, um Veränderungen in der Maschinenakustik zu detektieren, die auf mechanische Probleme hinweisen könnten.
-
Ölanalyse: Untersuchen Sie das Schmieröl auf Verunreinigungen und Verschleißpartikel, um den Zustand von Lagern und Getrieben zu überwachen.
Schritt 3: Implementierung der Software und Dateninfrastruktur
Die Implementierung eines leistungsfähigen Condition Monitoring Systems erfordert eine robuste Software- und Dateninfrastruktur. Dieser Schritt ist entscheidend, um die gesammelten Daten effektiv zu verarbeiten und auszuwerten.
Auswahl der Condition Monitoring Software
-
Anforderungen definieren: Basierend auf Ihren Zielen und den ausgewählten Monitoring-Methoden sollten Sie die Anforderungen an die Condition Monitoring Software klar definieren. Berücksichtigen Sie dabei Aspekte wie Benutzerfreundlichkeit, Skalierbarkeit und Integration mit bestehenden Systemen.
-
Softwareevaluation: Führen Sie eine Marktanalyse durch, um geeignete Condition Monitoring Softwarelösungen zu identifizieren. Berücksichtigen Sie dabei auch Referenzen und Erfahrungsberichte anderer Unternehmen im Maschinen- und Anlagenbau.
-
Pilotprojekt: Starten Sie mit einem Pilotprojekt, um die ausgewählte Software in einem kleineren Umfang zu testen und zu evaluieren. Dies hilft, potenzielle Probleme frühzeitig zu identifizieren und Anpassungen vorzunehmen.
Dateninfrastruktur
-
Datenintegration: Integrieren Sie die verschiedenen Datenquellen in eine zentrale Datenbank. Dies kann durch die Nutzung von Industrieprotokollen und Schnittstellen wie OPC UA, Modbus oder proprietären Schnittstellen der Maschinenhersteller erfolgen.
-
Datenverarbeitung: Stellen Sie sicher, dass die Daten in Echtzeit verarbeitet und analysiert werden können. Dies erfordert leistungsfähige Server und Datenbanklösungen.
-
Sicherheit und Datenschutz: Implementieren Sie Maßnahmen zur Sicherstellung der Datenintegrität und zum Schutz sensibler Informationen. Dies umfasst die Nutzung von Verschlüsselungstechnologien und Zugriffsmanagementsystemen.
Schritt 4: Schulung und Einbindung des Personals
Ein entscheidender Erfolgsfaktor für die Einführung eines Condition Monitoring Systems ist die Einbindung und Schulung des Personals. Nur durch ein gut geschultes und motiviertes Team kann das volle Potenzial eines Condition MOnitoring Software ausgeschöpft werden.
Schulungsmaßnahmen
-
Schulungskonzepte entwickeln: Erstellen Sie Schulungskonzepte, die auf die verschiedenen Zielgruppen zugeschnitten sind, z.B. Bedienpersonal, Instandhalter und Führungskräfte. Die Schulungen sollten sowohl theoretische als auch praktische Inhalte umfassen.
-
Training on the Job: Führen Sie Schulungen direkt an den Maschinen durch, um das Personal mit der praktischen Anwendung der Condition Monitoring Lösung vertraut zu machen. Nutzen Sie dabei reale Anwendungsfälle und Beispiele aus dem eigenen Betrieb.
-
Zertifizierungen: Bieten Sie Zertifizierungen an, um die Motivation der Mitarbeiter zu steigern und die Qualität der Schulungen zu gewährleisten.
Einbindung des Personals
-
Kommunikation: Informieren Sie das gesamte Team frühzeitig über die Einführung des Condition Monitoring Systems und die damit verbundenen Vorteile. Eine transparente Kommunikation hilft, mögliche Bedenken abzubauen und Akzeptanz zu schaffen.
-
Mitarbeiter einbinden: Beziehen Sie das Personal aktiv in den Implementierungsprozess ein. Nutzen Sie deren Erfahrungen und Kenntnisse, um das Condition Monitoring System optimal auf die spezifischen Anforderungen des Betriebs abzustimmen.
-
Feedbackkultur etablieren: Fördern Sie eine Feedbackkultur, in der Mitarbeiter ihre Erfahrungen und Verbesserungsvorschläge einbringen können. Dies hilft, das Monitoring System kontinuierlich zu optimieren und an die Bedürfnisse des Betriebs anzupassen.
Schritt 5: Kontinuierliche Verbesserung und Optimierung
Nach der erfolgreichen Einführung des Condition Monitoring Systems ist es wichtig, einen Prozess der kontinuierlichen Verbesserung und Optimierung zu etablieren. Dies stellt sicher, dass das Monitoring System langfristig effektiv bleibt und sich an veränderte Bedingungen anpasst.
Monitoring und Analyse
-
Regelmäßige Überprüfung: Überwachen Sie kontinuierlich die Leistungsfähigkeit des Condition Monitoring und überprüfen Sie regelmäßig die gesammelten Daten und deren Auswertungen.
-
Trendanalysen: Führen Sie Trendanalysen durch, um langfristige Entwicklungen zu erkennen und proaktiv auf mögliche Probleme reagieren zu können.
-
Benchmarking: Vergleichen Sie die Ergebnisse Ihres Condition Monitoring Systems mit Best Practices und Benchmarks aus der Branche, um Verbesserungspotenziale zu identifizieren.
Optimierung des Systems
-
Software-Updates: Halten Sie die Monitoring-Software stets auf dem neuesten Stand und nutzen Sie regelmäßig angebotene Updates und Erweiterungen.
-
Anpassung der Monitoring-Methoden: Passen Sie die verwendeten Monitoring-Methoden kontinuierlich an neue Erkenntnisse und technologische Entwicklungen an.
-
Mitarbeiterschulungen: Führen Sie regelmäßig Auffrischungsschulungen durch, um sicherzustellen, dass das Personal stets auf dem neuesten Stand ist und die Systeme effektiv nutzen kann.
Erfolgskontrolle
-
Kennzahlen und KPIs: Definieren Sie klare Kennzahlen und Key Performance Indicators (KPIs), um den Erfolg des Condition Monitorings zu messen. Beispiele hierfür sind die Reduzierung ungeplanter Ausfälle, die Verringerung der Wartungskosten und die Erhöhung der Maschinenverfügbarkeit.
-
Regelmäßige Berichterstattung: Erstellen Sie regelmäßige Berichte und Präsentationen, um die Ergebnisse der Condition Monitoring Lösung transparent darzustellen und den Nutzen für das Unternehmen zu verdeutlichen.
-
Anpassung der Zielsetzungen: Überprüfen Sie regelmäßig die ursprünglichen Zielsetzungen und passen Sie diese bei Bedarf an, um den sich ändernden Anforderungen und Rahmenbedingungen gerecht zu werden.
Fazit
Die Einführung eines Condition Monitoring Systems im Maschinen- und Anlagenbau ist ein komplexer Prozess, der jedoch erhebliche Vorteile für die Instandhaltung und den Betrieb bieten kann. Durch eine gründliche Bestandsaufnahme, die Auswahl geeign
eter Monitoring-Methoden, die Implementierung einer robusten Dateninfrastruktur, die Schulung und Einbindung des Personals sowie die kontinuierliche Verbesserung und Optimierung können Unternehmen ihre Maschinenverfügbarkeit erhöhen, Wartungskosten senken und ungeplante Ausfälle minimieren.
Die fünf Schritte zur Einführung eines Condition Monitoring Systems, wie in diesem Artikel beschrieben, bieten eine praxisnahe Anleitung, um diesen Prozess erfolgreich zu gestalten. Als Verantwortlicher für die Instandhaltung liegt es in Ihrer Verantwortung, diesen Wandel aktiv zu gestalten und Ihr Team auf diesem Weg zu unterstützen. Nutzen Sie die Chancen, die ein Condition Monitoring System bietet, und treiben Sie die Digitalisierung und Effizienzsteigerung in Ihrem Unternehmen voran.